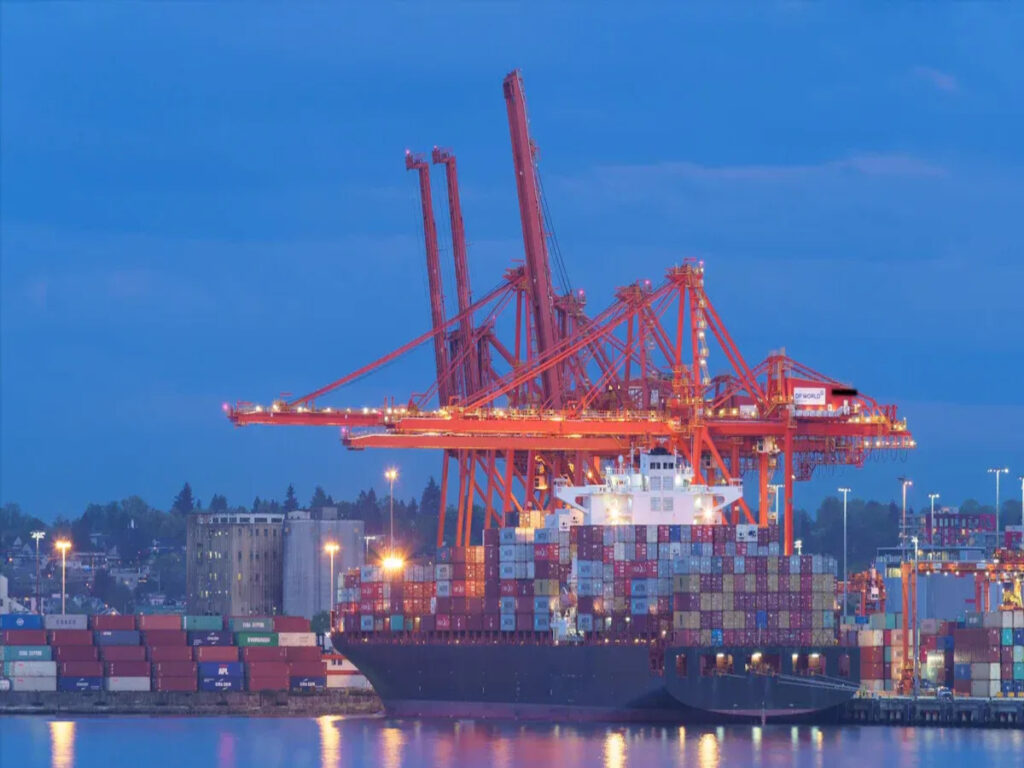
Proper materials, clear labelling, and thorough paperwork are essential for safety and compliance for all importers selling stop signs for sale in Australia. Importers must adhere to strict regulations. Australian standards require careful vehicle guidance and defect inspections. Failure to comply with these rules can result in severe penalties, including fines or imprisonment. The table below outlines the maximum penalties for non-compliance:
Offence Category | Maximum Penalty (Individuals) | Maximum Penalty (Body Corporate) |
---|---|---|
Industrial Manslaughter | 20 years imprisonment | $10 million fine |
Reckless Conduct | $300,000/5 years imprisonment | $3 million fine |
Failure to Comply | $150,000 | $1.5 million fine |
Importers should understand that adhering to standards, safety procedures, and documentation requirements ensures vehicle safety. It also prevents recalls and supports importers in maintaining high standards. Proper guidance, defect inspections, and compliance with standards protect drivers and the public. Importers committed to following regulations, maintaining accurate paperwork, and prioritising safety reduce the risk of recalls and uphold confidence in vehicle and road safety.
Takeaway chiave
- Importers must follow strict Australian rules for stop signs. These rules cover size, forma, reflectivity, Materiali, and labelling. This helps keep roads safe and meets the law.
- Proper paperwork is needed, like Certificates of Conformity and test reports. Accurate shipping papers are also important. This stops customs delays, fines, or product recalls.
- Using trusted suppliers is important. Doing careful checks before shipping helps find problems early. This lowers the chance of expensive recalls.
- Keeping up with new safety rules is important. This helps importers follow the law and keeps road users safe.
- Not following the rules can cause big problems. You could get fines, recalls, or even go to prison. COSÌ, safety and correct steps are very important for a good import business.
Compliance and Safety
Why Compliance Matters
Compliance is the base of import safety for all importers. Australian rules set tough standards for stop signs. These rules help keep drivers and the public safe. The standards make sure each sign is easy to see, dura a lungo, and does not have defects. Importers must follow safety rules to stop unsafe products from reaching the market. Authorities give advice to help importers learn the rules and stay safe at every step.
Importers who care about safety lower the chance of defects. They help keep vehicles safe by using good practices and following the rules. Safety steps include checking for defects, using correct labels, and picking approved materials. Importers who do these things help keep all vehicles on Australian roads safe.
Nota: Safety compliance is not a choice. Every importer must follow it if they want to supply stop signs for vehicles.
Legal and Safety Risks
Not following safety rules brings big legal and safety problems. Authorities might stop unsafe products at customs or ban them from use. Importers who ignore safety rules can get fines or face legal trouble. If there are defects, recalls can happen. This can hurt the importer’s name and put drivers in danger.
Unsafe stop signs can confuse drivers. This can lead to more accidents and put people at risk. Importers need to know that safety rules protect their business and the public. Checking for defects, following rules, and getting advice from experts help importers stay safe.
Importers who follow safety rules make sure every stop sign is top quality. They help keep vehicles safe, stop defects, and protect the road system. Safety rules are the most important part of importing responsibly.
Standards for Stop Signs
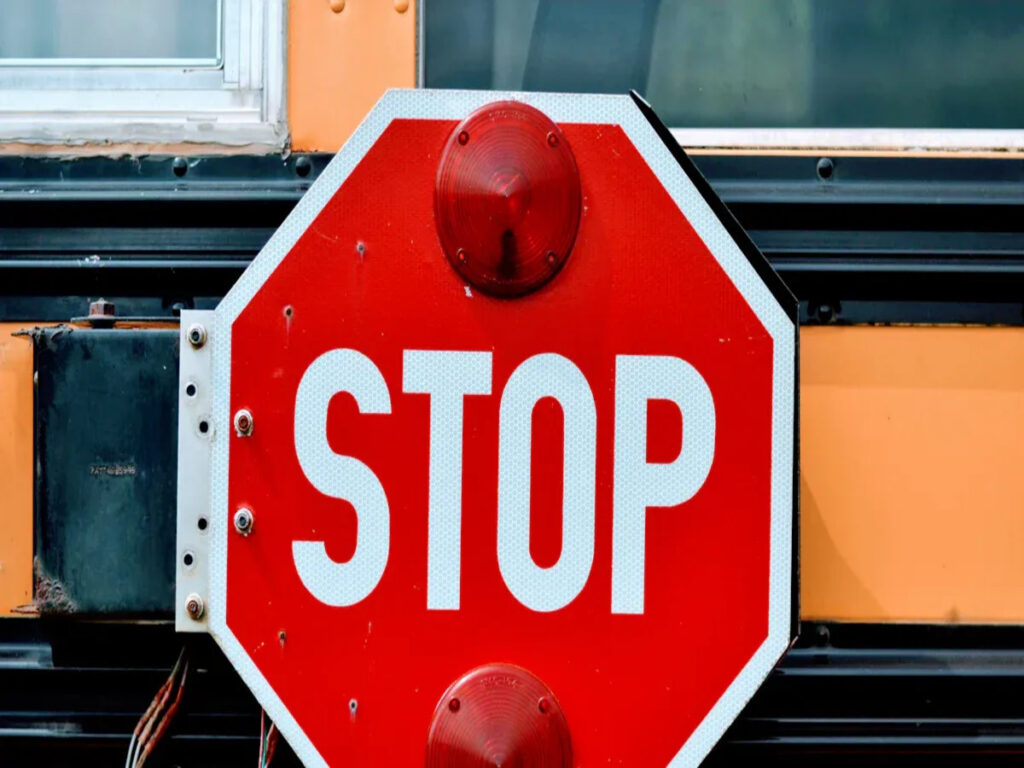
Standard australiani
Australian rules have very strict requirements for stop signs. Every importer needs to know these rules before bringing signs into Australia. The main documents are COME 1742.2 E AS/NZS 1906.1. These documents explain everything about stop signs, like shape and materials. They help keep all road users safe.
- Shape and Size: The stop sign must be an octagon. Most roads use a 750 mm sign. High-speed roads use a 900 mm sign. These sizes make the sign easy to see.
- Riflettività: The sign must use Class 1 or Class 1W reflective sheeting. This material meets safety rules. It helps drivers see the sign at night or in bad weather.
- Language and Text: The word “FERMARE” must be in big capital letters. No other words or symbols are allowed. This rule makes the message clear and safe.
- Materiali: The sign must be made from aluminium or galvanised steel. These materials do not rust and last in tough weather. The coating must stop UV rays so the sign does not fade.
- Labelling: Each sign must show the supplier’s name, reflectivity class, compliance code, and batch number. This labelling helps track signs and check for defects.
Importers must follow these rules to meet safety standards. If they do not, customs can reject the signs or ban them. Every car on the road needs clear, forte, and easy-to-see stop signs to stay safe.
Nota: Australian standards keep people safe by making sure every stop sign is high quality. Importers who do not follow these rules can get fines or have their products recalled.
International Standards Comparison
Importers sometimes look at Australian rules and compare them to other countries. The most common one is the MUTCD, which sets rules in the United States. The MUTCD wants all signs to look the same and be easy to read.
Caratteristica | Standard australiani (COME 1742.2, AS/NZS 1906.1) | MUTCD (U.S.A.) |
---|---|---|
Forma | Octagon | Octagon |
Standard Size | 750 mm / 900 mm | 750 mm (30 In) / 900 mm (36 In) |
Riflettività | Classe 1 / 1W (AS/NZS 1906.1) | ASTM Type XI or higher |
Language | English only, “FERMARE” in uppercase | English only, “FERMARE” in uppercase |
Materiali | Aluminium or galvanised steel, Resistente ai raggi UV | Alluminio, various reflectivity |
Labelling | Supplier, batch, compliance code | Not always required |
Many importers think MUTCD signs will work in Australia. This is not correct. Australian rules have special requirements for reflectivity, labelling, and defect checks. Signs from the US may not pass Australian safety checks. Importers who use MUTCD rules might not follow the law and could have their signs stopped at customs.
Road safety depends on clear and matching rules. Studies show drivers do better with signs that all look the same. When importers follow the rules, they lower the chance of defects and make roads safer. Experts say importers should always follow local rules. This helps stop accidents from confusion or hard-to-see signs.
- Drivers need stop signs that meet federal motor vehicle safety standards.
- Using the same rules everywhere helps drivers trust the signs.
- Importers who do not follow local rules can get fines, recalls, or lose trust.
- Safety rules protect every driver from confusion and unsafe signs.
Mancia: Importers should always check local rules before buying stop signs. Using the wrong rules can cause delays and make roads less safe.
Materials and Manufacturing
Reflectivity Requirements
Reflectivity is very important for stop sign safety. Importers must follow strict rules so signs are always easy to see. Australian standards say signs need Class 1 or Class 1W reflective sheeting. These materials help drivers spot stop signs at night or in bad weather. Good reflectivity lowers the chance of car crashes and helps meet safety rules.
The table below shows important test results for reflectivity:
Study/Researcher | Test Type | Key Numerical Results | Notes |
---|---|---|---|
Morales (1983) | Retroreflectivity test | Minimum 40 cd/lx/m² for 30-inch STOP signs | Weighted sum of red and white values |
Mace et al. (1985) | Luminance and recognition | 18 cd/lx/m² (low complexity), 36 cd/lx/m² (high) | Luminance affects recognition |
Schmidt-Clausen (1985) | Scale model luminance test | Optimal: 10-35 cd/m²; Max: ~60 cd/m² | Legend luminance for best performance |
Australian study (1991) | Field retroreflectivity | Minimum: 9.7 cd/m²; Optimal: 23 cd/m² | Terminal retroreflectivity for effectiveness |
Sivak and Olson (1985) | Meta-analysis | Optimal: ~75 cd/m²; Retroreflettività: 3547 cd/lx/m² | Contrast ratio 12:1 for full reflectorisation |
Importers who meet these rules help stop defects and keep vehicles safe. Following these standards means shipments are less likely to be rejected.
Substrate and Durability
The substrate is the main part of every stop sign. Importers must pick materials that last long and can handle tough weather. Aluminium is the best choice for public roads because it does not rust and lasts a long time. ORALITE 5500 Engineer Grade Reflective Vinyl, Per esempio, lasts seven years outside. This material stands up to sun and rain, so it works well for vehicle safety.
Other substrates, like high-density urethane foam, last over ten years outdoors. Aluminium composite material is light but still strong. Importers should not use expanded PVC, as it does not work well outside and can cause defects. Picking the right substrate helps meet safety rules and makes sure every vehicle gets clear signs.
Labelling for Compliance
Good labelling is needed for safety and following the rules. Importers must make sure each stop sign shows the supplier’s name, reflectivity class, compliance code, and batch number. These details help authorities find defects and check if signs are safe.
Research from the Federal Highway Administration says clear labelling, like STOP AHEAD pavement markings, helps drivers follow the rules and lowers crashes. These markings give drivers a clear warning, so they see stop signs and react safely. Importers who follow labelling rules help keep roads safe and avoid recalls from defects.
Mancia: Importers should always check labels before shipping. Correct labelling keeps vehicle users safe and helps meet Australian standards.
Importer Documentation
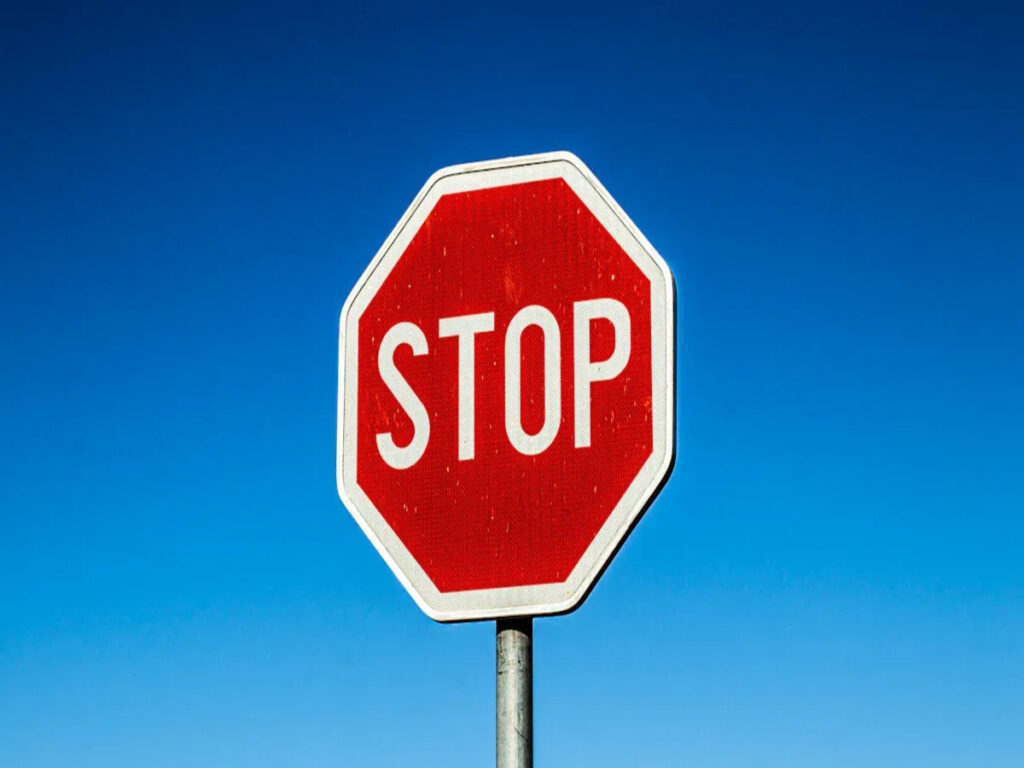
Certificates and Test Reports
Importers must get the right certificates and test reports before sending stop signs to Australia. These papers show that each sign meets strict safety rules. The Certificate of Conformity (CoC) proves the product passed all needed tests. Material specification sheets from the sheeting maker show the reflective material meets Australian standards. Test reports from trusted labs prove the stop signs are strong, reflective, and can handle bad weather.
Importers can also ask for extra papers like ISO certification or factory inspection reports. These extra records show the maker uses good quality checks and follows the rules. By collecting these papers, importers can prove to customs that every stop sign is safe for vehicles.
Mancia: Always keep both digital and paper copies of all certificates and test reports. Having these ready helps answer questions during customs checks.
Shipping and Customs Papers
Importers need correct shipping and customs papers for every shipment. Customs officers need several important documents for each group of stop signs:
- Certificate of Origin (COO): Shows where the stop signs were made. This matters for import rules and trade deals.
- Commercial Invoice (CI): Lists the buyer and seller, describes the goods, gives the amount, where they came from, price, and HS codes, and must be signed.
- Export Declaration: Needed for big shipments or those needing export licences. Sent online to follow export rules.
- Shipping Invoice: Gives details about the shipment and helps with customs.
- HS Code: Puts the product in the right group for customs and taxes.
- Country of Origin Declaration: Says where the goods were made.
- Additional Documents: Sometimes customs want a Dangerous Goods Declaration or Custom Package Document.
Importers can get into trouble if they make mistakes in these papers. Customs officers expect importers to be careful, even if mistakes are not on purpose. Wrong HS codes, wrong values, or missing country details can mean huge fines. Goods might be taken away, and importers could be banned from importing again. Customs checks can last years if papers are wrong. These tough rules show why it is important to be correct at every step.
Nota: Customs rules need exact details like country of registry, related party deals, and charges. Importers must give the right facts or good guesses, with proof ready fast. Not following the rules can mean forms are rejected, delays, and fines.
Labelling and Traceability
Labelling and traceability are key for following the rules when importing stop signs. Each stop sign must have clear labels with the supplier’s name, reflectivity class, compliance code, and batch number. This lets officers trace each sign back to where it came from, making sure it is safe for vehicles.
Traceability uses special codes and batch tracking. Importers must keep full records from the maker to delivery. These records include receipts, special numbers, and transport logs. Outside checks by certifiers often look at these records to make sure rules are followed. Auditors use a risk plan, sometimes visiting places or checking papers to see if best practices are used.
Digital tools, like online systems and blockchain, now help importers keep good records and stop fraud. Careful checks and risk steps, like supplier risk scores and ways to fix problems, help with traceability and labelling. These steps help stop delays at the border and protect the importer’s good name.
Callout: Good records and traceability stop import delays and make sure every stop sign meets Australian safety rules. Importers who do this help keep people safe and keep trust in the vehicle sector.
Customs and Import Process
Quarantine and Inspection
Australian customs officers look at every stop sign shipment. They check each vehicle used to move the signs. Officers look for bugs or dirt on the packaging. They follow strict rules to keep out dangerous pests. Importers must clean all goods before they ship them. If officers find a risk, they can hold the shipment. They also check if labels are in the right place. Each stop sign must meet safety standards. If a sign does not pass, the importer may have to recall it. This helps keep all vehicles and roads safe.
Duties and Declarations
Importers must tell customs about every stop sign shipment. They give papers that show where the signs are from, their value, and where they will go. Customs officers use this to work out taxes and duties. Importers must follow all safety rules for importing. If they give wrong details, they can get fines or face a recall. Officers also check if the stop signs are safe for vehicles. Importers who follow the rules avoid delays and keep a good name. Correct paperwork helps keep things safe and stops problems with recalls or placement.
Public vs Private Use
Australia has different rules for public and private stop sign use. Public roads need strict safety standards. Every stop sign must follow the rules for vehicles. Councils and road groups check where signs are placed. They can order a recall if a sign does not meet the rules. Private places, like car parks, have more freedom. Ancora, importers should use safe signs. Insurance may not pay if a bad sign causes a crash. Importers who use the right signs and follow the rules help keep vehicles safe and avoid costly recalls.
Mancia: Importers should always check the newest rules before shipping. Following the rules keeps imports safe and protects every vehicle.
Best Practices for Importers
Supplier Verification
Importers need to pick suppliers very carefully. Good suppliers help stop defects and lower recall risks. Importers should ask for certificates to show the supplier meets safety standards. It is smart to check if the supplier had problems before. Importers can talk to others who bought from the supplier. This helps find out if the supplier follows safety rules. Visiting the supplier’s factory is a good idea. This lets importers see how the supplier works and if they meet safety needs.
Pre-Shipment Checks
Importers must check stop signs before shipping them. These checks help find defects that could cause recalls. Every batch should be checked for safety. Importers need to test reflectivity and look for defects. They should also check labels to make sure they follow the rules. Using a checklist helps importers remember every step. These checks make sure stop signs are safe to use. Skipping these steps can lead to recalls and safety problems.
Mancia: Doing checks before shipping lowers the chance of defects and recalls. These steps help keep vehicles safe.
Staying Updated
Importers must keep up with new safety rules. They should check official websites for updates. IL Queensland Department of Transport and Main Roads has the latest rules. This site gives news about AS 1742 and other standards. Importers should set reminders to check for updates often. Checking rules often helps importers avoid problems. Importers who do this keep vehicles safe and have good safety records.
Best Importer Practices | Safety Focus | Recall Prevention | Guidance Provided |
---|---|---|---|
Supplier Verification | SÌ | SÌ | SÌ |
Pre-Shipment Checks | SÌ | SÌ | SÌ |
Staying Updated | SÌ | SÌ | SÌ |
Nota: Importers who follow these best practices keep vehicles safe. They avoid defects and lower the chance of recalls. Good steps and guidance help keep the motor sector safe.
Common Pitfalls
Incomplete Documentation
Many importers have trouble when they do not have all their papers ready. Customs officers in Australia check every paper to make sure rules are followed. If papers are missing or wrong, shipments can be delayed or sent back. Importers must include certificates, test reports, and shipping invoices for every product used with vehicles. Good habits help stop mistakes. Each importer should use a checklist for all needed papers. This list helps keep things safe and follows the rules at every step.
Nota: If papers are missing, there can be fines or recalls. Importers who use good habits keep their business and the motor sector safe.
A table can help importers keep track of their papers:
Document Type | Needed For Compliance | Supports Safety | Prevents Recall |
---|---|---|---|
Certificate of Conformity | SÌ | SÌ | SÌ |
Test Report | SÌ | SÌ | SÌ |
Shipping Invoice | SÌ | SÌ | SÌ |
Importers who use these steps lower the chance of safety problems. They also show they care about vehicle safety and follow the rules.
Non-Compliant Products
Non-compliant products bring big risks for every importer. Products that do not meet the rules can cause a recall or a safety recall plan. Importers must check every stop sign to make sure it follows the rules before shipping. Testing finds any problem that could make vehicles unsafe. If a product fails a test, it may have safety problems that put the motor sector in danger.
Importers should use strict checks for quality. They must follow all rules and test each batch to make sure it is right. A recall can hurt an importer’s name and cause legal trouble. Safety is the most important thing for every vehicle on the road. Importers who do not follow the rules may face a safety recall plan or lose their licence to import motor products.
Mancia: Importers should always check their safety recall plan and update their steps to match new rules. This keeps every vehicle and motor product safe from problems or recalls.
Importers have to follow all the rules for stop signs for sale. Using good habits keeps vehicles safe and lowers the chance of recalls. Experts can give advice to help importers follow safety rules. Importers should always check the standards, pick trusted suppliers, and talk to local authorities. The right stop signs for sale help keep vehicles safe and support the motor sector. Studies show that good habits and advice lower recalls and make roads safer. Importers who follow the rules help stop accidents and keep roads safe.
- Importers need to use the right size and put stop signs in the correct place.
- Importers should follow advice about how easy the sign is to see and what reflective materials to use.
- Importers must not use stop signs to slow down cars.
- Importers need to check the height and distance for each area where vehicles go.
- Importers should use reflective sheeting to keep things safe and stop recalls.
Advice and good habits help importers keep vehicles and motor products safe from recalls and support the motor sector.
Domande frequenti
What documents must an importer provide for stop sign shipments?
Importers need to give several papers for each shipment. They must have a Certificate of Conformity and material specification sheets. A commercial invoice is also needed. Importers must include the HS code and a country of origin declaration. These papers help customs check if the stop signs follow Australian rules.
Can an importer use US-style stop signs in Australia?
US-style stop signs are not allowed on public roads in Australia. The signs must follow AS 1742.2 e AS/NZS 1906.1. If signs do not meet these rules, customs can stop them. They might also not be allowed to be put up.
How does an importer ensure stop signs meet reflectivity standards?
Importers should ask the maker for test reports. These reports must show the sheeting meets Class 1 or Class 1W. Checking often and picking good suppliers helps keep things right.
Are there different rules for stop signs used on private property?
Private property has more freedom with stop signs. Ancora, it is best to use signs that follow the rules. Insurance and councils may still want signs to meet Australian standards if something goes wrong.
What happens if stop signs arrive with incomplete paperwork?
Customs can hold or send back the shipment. The importer might get a fine or face more checks. Having all the right papers helps things go smoothly and stops costly delays.