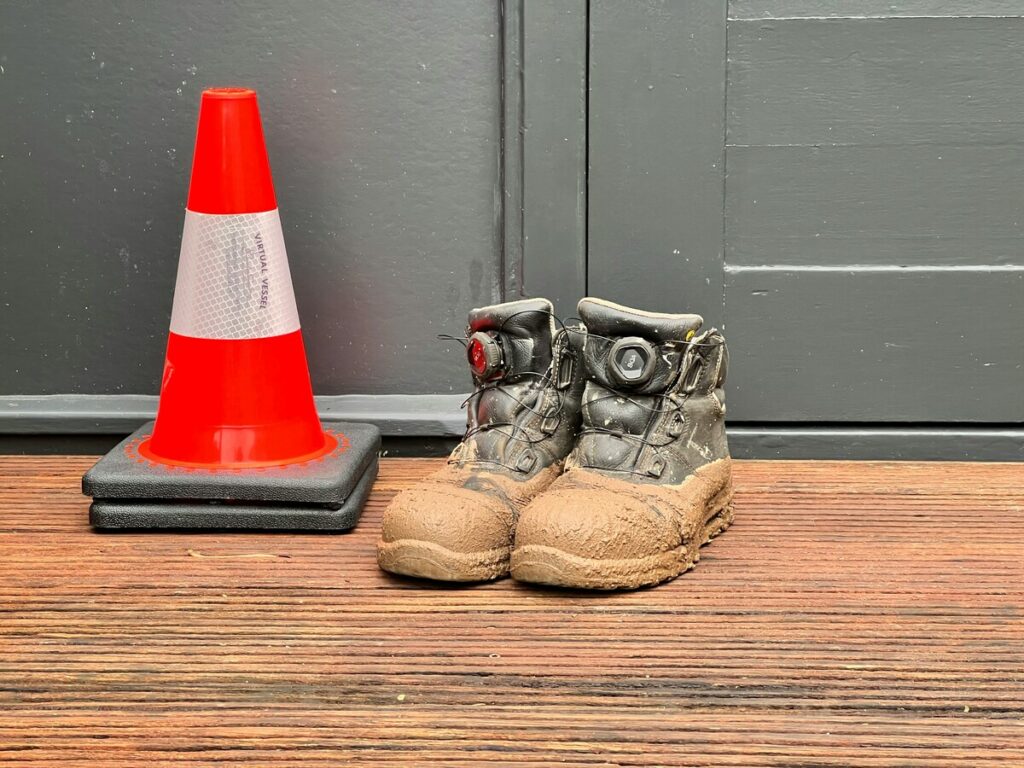
Lead paint poses a serious hazard during renovation projects, especially in older buildings. You must prioritize worker safety to prevent harmful exposure. Lead dust and chips can spread quickly, creating risks for both workers and the public. Using colored cones helps you establish clear boundaries around work zones. These colored cones guide workers and alert others to potential hazards. They also create a safer environment by keeping unauthorized individuals away from dangerous areas. By taking these precautions, you protect everyone involved in the project.
Conos de tráfico de Optsigns are designed to enhance safety, with high visibility and durability to help you manage hazardous zones effectively, ensuring a safer workspace for both workers and passersby.
Introduction to Lead Paint Risks in Older Homes
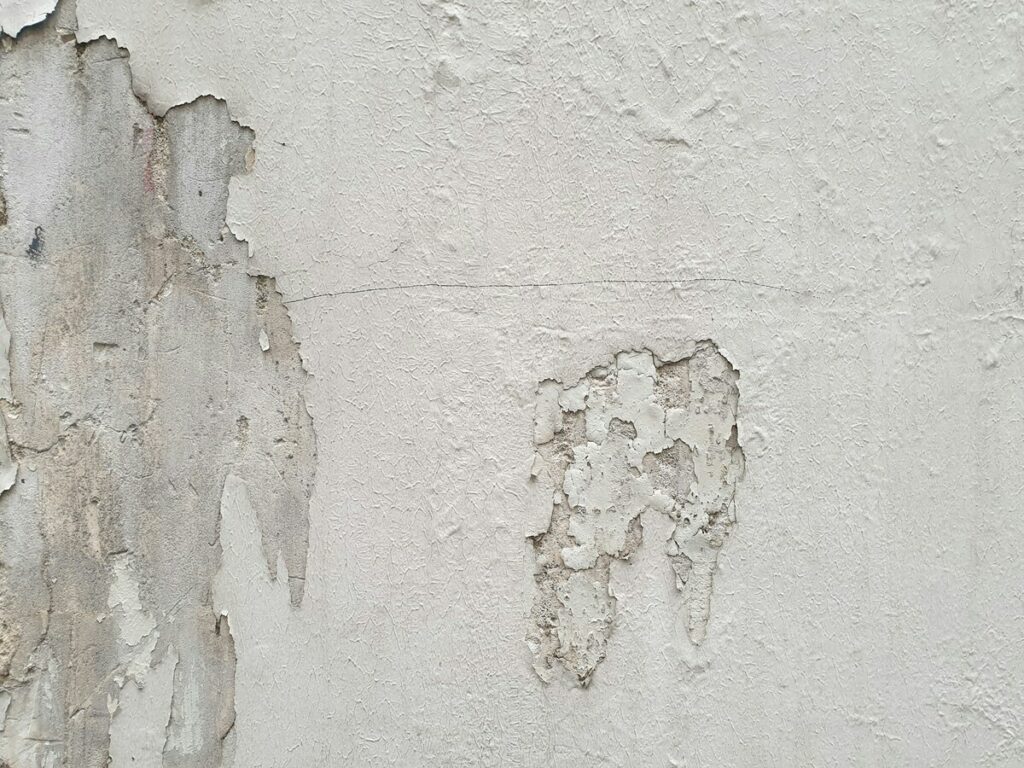
The Prevalence of Lead Paint in Older Buildings
Many older homes, especially those built before 1978, contain lead-based paint. During that time, lead was a common ingredient in paint due to its durability and vibrant finish. Sin embargo, this paint becomes a serious problem as it deteriorates. Cracking, peladura, or chipping paint releases hazardous materials into the environment. Renovation projects in these homes often disturb the paint, increasing lead exposure risks for workers and residents.
You should always assume that homes built before 1978 contain lead-based paint unless testing proves otherwise. Even small amounts of lead dust can spread quickly, contaminating surfaces and posing health risks. Identifying and addressing these risks is essential before beginning any renovation work.
Health Impacts of Lead Exposure
Lead exposure risks affect both children and adults, but children are especially vulnerable. Lead can harm their developing brains and nervous systems, leading to long-term issues. Common health problems in children include slowed growth, learning difficulties, and behavioral challenges. They may also experience hearing and speech problems, lower IQ, and trouble concentrating.
Adults face different health concerns. Prolonged exposure can cause high blood pressure, nerve disorders, and memory problems. It may also lead to muscle and joint pain or reproductive issues. The table below highlights the health impacts of lead exposure:
Group | Health Issues |
---|---|
Niños | Lowered IQ, Damage to the brain and nervous system, Learning and behavioral difficulties, Slowed growth, Hearing problems, Headaches |
Adults | Reproductive problems, High blood pressure and hypertension, Nerve disorders, Memory and concentration problems, Muscle and joint pain |
Understanding these risks emphasizes the importance of handling lead and other hazardous materials with care. Protecting yourself and others from lead exposure should always be a top priority during renovation projects.
Understanding EPA Renovation, Repair, and Painting (RRP) Normas
Overview of EPA’s Lead Paint Regulations
The EPA’s Lead Renovation, Repair, and Painting (RRP) Rule plays a critical role in protecting you and others from lead exposure during renovation projects. This regulation, fully effective since April 22, 2010, requires workers to follow lead-safe practices to minimize hazards. If you work on homes, escuelas, or child care facilities built before 1978, you must comply with these rules.
The RRP Rule mandates that workers and firms obtain certification. Certified renovators must complete training in lead-safe work practices. During renovation, you must ensure that dust and debris stay contained within the work area. These steps help prevent lead contamination and protect everyone involved.
Key provisions of the RRP Rule include:
- Certification for contractors working on projects that disturb lead-based paint.
- Specific work practices to reduce lead dust and debris.
- Responsibility for certified renovators to maintain a safe and clean work environment.
By adhering to these regulations, you can significantly reduce the risks associated with lead exposure.
Differences Between EPA and HUD Regulations
While both the EPA and HUD aim to address lead hazards, their regulations differ in several ways. Understanding these differences helps you comply with the appropriate standards for your project.
Stage of Job | Requisito | HUD LSHR | EPA RRP |
---|---|---|---|
Capacitación | Worker and supervisor training requirements | HUD requires all workers to complete a HUD-approved curriculum. | EPA certifies firms and requires one certified renovator on-site. |
End of Job | Post-renovation verification | HUD mandates clearance examinations by an independent party. | EPA allows cleaning verification by the renovator. |
Notification to Occupants | Informing residents about lead hazards | HUD requires notices to occupants within 15 days of lead hazard evaluation. | EPA does not require notification for non-owner residents. |
These distinctions highlight the unique approaches of each agency. Por ejemplo, HUD focuses on independent clearance testing, while the EPA emphasizes on-site cleaning verification. Knowing these differences ensures you meet the correct requirements for your renovation project.
Identifying Lead Paint and Safe Work Setup
How to Identify Lead-Based Paint in Older Buildings
Identifying lead-based paint in older buildings is a critical first step in ensuring safety during renovation projects. You can use several effective methods to determine if lead-based paint is present. Start with a visual inspection. Look for multiple layers of paint, especially in homes built before 1978. Cracking, peladura, or chipping paint often signals potential lead hazards.
For a more accurate assessment, consider using lead paint test kits. These kits, available at most home improvement stores, allow you to test surfaces quickly. Follow the instructions carefully to get reliable results. If you need a more thorough evaluation, hire EPA-certified professionals. They use specialized tools and techniques to identify lead-based paint and ensure safe handling. This step is especially important if you suspect extensive contamination.
By identifying lead-based paint early, you can take the necessary precautions to protect yourself and others from exposure.
Properly Setting Up a Safe Work Environment with Colored Cones
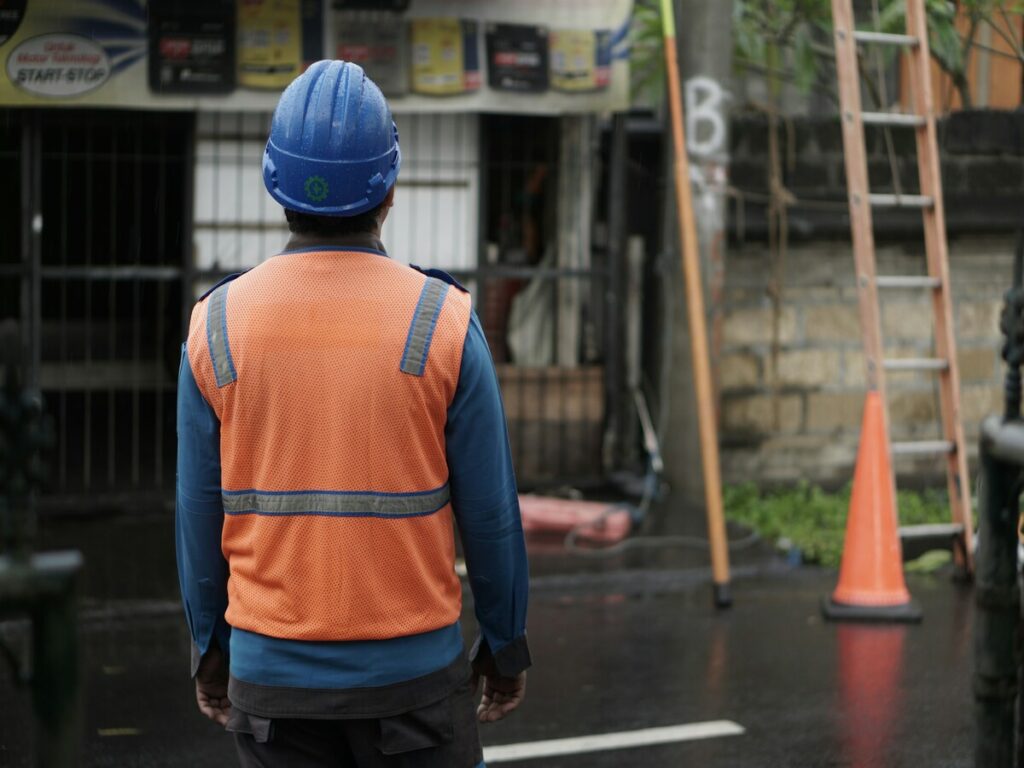
Once you identify lead-based paint, setting up a safe work environment becomes essential. Colored cones play a vital role in creating a secure workspace. Use these colored cones to mark the boundaries of the work zone clearly. This helps keep unauthorized individuals away from hazardous areas and ensures workers stay within designated spaces.
Place the colored cones strategically around the worksite. Por ejemplo, use brightly colored cones to highlight entrances, salidas, y zonas restringidas. This visual barrier minimizes the risk of accidental exposure to lead dust or debris. Combine this setup with lead-safe work practices to enhance safety. Cover floors and furniture with plastic sheeting to prevent contamination. Seal off doors and vents to stop lead dust from spreading to other areas.
Colored cones also serve as a constant reminder for workers to follow lead-safe work practices. They reinforce the importance of maintaining a clean and organized workspace. Mediante el uso de estas herramientas de manera efectiva, you create a safer environment for everyone involved in the renovation.
Con OPTsigns conos de trafico, you can ensure that safety is a priority at all times. Designed for both durability and high visibility, these colored cones help keep hazardous areas clearly marked, allowing workers to stay focused on the task at hand while minimizing risks.
Worker Protection and Dust Reduction
Worker Safety Measures When Handling Lead Paint
Protecting yourself from lead hazards requires proper Equipo de protección personal (PPE). Lead exposure can occur through inhalation or contact with contaminated surfaces, so wearing the right gear is essential. The level of PPE you need depends on the concentration of lead in your work environment. Use the table below to determine the appropriate equipment:
Lead Concentration (Micrograms) | Required PPE |
---|---|
50 or fewer | Half mask respirator with air purification and high-efficiency filters |
50 a 250 | Full mask with air purification and filters |
250 a 500 | Powered purifying respirator mask with high-efficiency filters or half mask with air delivery system in positive pressure mode |
500 a 1000 | Full face mask with air delivery system, including a hood, helmet, or full-body suit in positive pressure mode |
1000 or greater | Self-contained breathing apparatus (SCBA) operating in positive pressure mode |
Additional PPE | Non-permeable gloves, coveralls, boots, goggles, and eyewash stations may be required depending on the situation. |
Always inspect your PPE before use to ensure it is in good condition. Replace damaged or worn-out equipment immediately. These safety precautions reduce the risk of exposure and keep you safe during renovation projects.
Procedures for Reducing Lead Dust
Minimizing lead dust is critical for worker safety and public health. Follow these best practices to control dust during renovation activities:
- Remove furniture, rugs, curtains, and other household items from the work area until cleanup is complete.
- Wrap immovable items tightly with plastic sheeting and seal them with tape.
- Cover floors with plastic sheeting to catch dust and debris.
- Close and seal all doors in the work area to prevent dust from spreading.
- Turn off forced-air heating and air conditioning systems, and cover vents with plastic sheeting.
- Mist surfaces with a spray mister or pump sprayer before sanding, scraping, drilling, or cutting to suppress dust.
- Usar un HEPA vacuum cleaner frequently to clean the work area and remove fine particles.
These steps help contain lead dust and protect everyone involved in the project. By combining these procedures with proper PPE, you create a safer environment and reduce the risks associated with lead exposure.
Maintaining a Clean Work Area and Proper Waste Disposal
Keeping Work Zones Clean and Safe
Maintaining a clean work zone is essential to minimize lead hazards during renovation projects. A clean environment reduces the risk of lead dust spreading and protects everyone involved. Follow these steps to ensure your work area remains safe and organized:
- Use HEPA-rated dust vacuums and exhaust systems for all machinery to capture fine particles effectively.
- Clean your work area at the end of each day until no dust, escombros, or residue remains.
- Mop uncarpeted floors thoroughly after completing the project to remove any remaining contaminants.
- Clean walls with a HEPA vacuum or a damp cloth to eliminate dust buildup.
- Vacuum all remaining surfaces and objects with a HEPA vacuum to ensure thorough cleaning.
- Wipe down all surfaces with wet disposable cleaning cloths. Continue wiping until the cloths come away clean.
These practices help you maintain a safe and dust-free environment, reducing the risks associated with lead exposure.
Proper Disposal of Lead-Contaminated Waste
Proper disposal of lead-contaminated waste is crucial to prevent environmental contamination and comply with legal requirements. The United States has specific guidelines for managing lead-based materials. The table below outlines key aspects of these regulations:
Aspecto | Descripción |
---|---|
Residential lead-based paint | Contractors can manage residential lead-based paint as household waste to reduce lead poisoning. |
Disposing of lead-contaminated items | Specific guidelines exist for the disposal of lead-contaminated toys and other household items. |
Lead-acid battery recycling | Regulations are in place for the recycling of lead-acid batteries, categorized as universal waste. |
Always follow local and federal regulations when disposing of lead-contaminated materials. Use sealed, heavy-duty bags to contain waste securely. Label the bags clearly to indicate their contents. Transport the waste to an approved disposal facility to ensure safe handling. By adhering to these practices, you protect the environment and comply with legal standards.
Clean-Up and Clearance Verification
Post-Renovation Clean-Up Procedures
After completing a renovation project, you must clean the work area thoroughly to eliminate lead hazards. A proper clean-up ensures the safety of workers, residents, and the surrounding environment. Follow these steps to achieve a lead-safe space:
- Clean walls by vacuuming them with a HEPA vacuum or wiping them down with a damp cloth.
- Vacuum all remaining surfaces and objects in the work area using a HEPA vacuum cleaner.
- Wipe all surfaces and objects with a damp cloth to remove any lingering dust.
- Mop uncarpeted floors thoroughly to capture any remaining contaminants.
- Perform a visual inspection to confirm that no dust, escombros, or residue remains.
- Use disposable cleaning cloths for a final check. Compare the results to a cleaning verification card to ensure the area meets safety standards.
Además, maintain cleanliness throughout the project. Place trash in heavy-duty plastic bags as you work. Vacuum the area frequently and clean your tools daily. Wash your hands and face during breaks and at the end of the day. Dispose of or clean your personal protective equipment properly. These practices help you minimize lead exposure and maintain a safe workspace.
Lead Clearance and Verification
Once the clean-up is complete, you need to verify that the area is free from lead hazards. Lead clearance verification involves inspecting the property to ensure no dust, escombros, or lead contamination remains. A lead dust wipe analysis is a common method used for this purpose. This test measures the amount of lead dust on surfaces to confirm that the area is safe.
En conclusión, safeguarding workers from lead paint hazards on renovation sites is crucial for both their health and safety. By following proper identification, protective measures, and clean-up procedures, contractors can significantly reduce the risk of lead exposure. Traffic colored cones play a vital role in this process, helping to create clear boundaries, control access to hazardous areas, and guide workers and pedestrians safely around the work zone. By incorporating traffic cones into a comprehensive safety plan, you can not only ensure regulatory compliance but also provide a safer work environment for all involved.