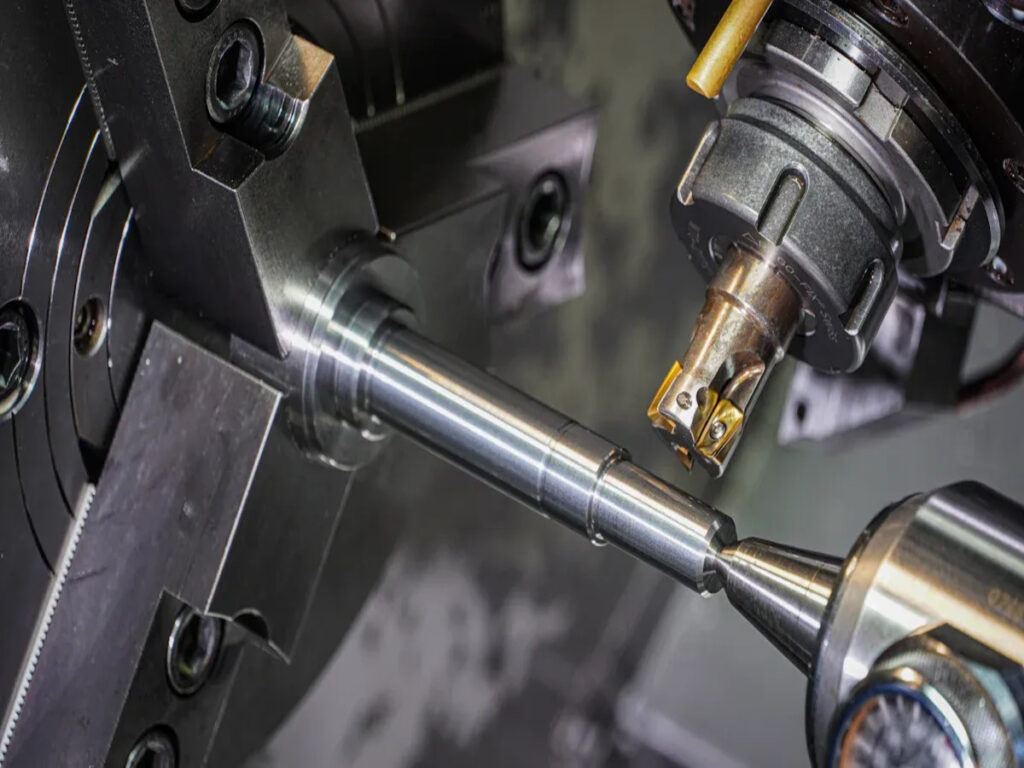
Metal sign brackets are important for holding signs and looking good. These traffic sign brackets keep signs steady and make them look better. Making them right is key for strength and lasting use.
- Good materials help make strong and useful brackets.
- Smart methods keep quality high and meet market needs.
- Better checks lower mistakes and build customer trust.
By caring about these things, metal brackets can last long and work well. They are also made to look great.
Key Takeaways
- Pick the best materials for metal brackets. Steel, aluminum, and stainless steel work well for different jobs.
- Use smart ways to make brackets. Tools like CNC machines and robots help make them better and faster.
- Focus on quality checks. Test and inspect often to keep brackets safe and strong.
- Design brackets to match needs. Choose materials and looks that work and look good.
- Keep track of materials and suppliers. This helps ensure quality and fix problems quickly.
Materials for Metal Sign Brackets

Common Metals for Metal Brackets
Metal sign brackets are made from different metals, each with special uses. Common choices include steel, aluminum, and stainless steel. Steel is very strong, making it great for heavy tasks. Aluminum is light and doesn’t rust, so it works well where weight matters. Stainless steel is strong and resists rust, making it good for both indoor and outdoor use.
Some metal sign brackets, like industrial ones, need to handle heavy loads. For commercial brackets, how they look and their finish are more important.
Characteristics of Common Metals:
- Steel: Very strong and lasts a long time.
- Aluminum: Light and doesn’t rust easily.
- Stainless Steel: Strong and resists rust very well.
Tests show thicker steel brackets hold more weight. For example, one bracket can hold up to 28.37 kN, proving its strength for tough jobs.
Properties of Materials for Custom Metal Brackets
Custom brackets are made for specific needs. You can pick materials based on strength, hardness, or rust resistance. Some custom brackets are 3D-printed, which allows for detailed designs. This method adds features like undercuts that improve how well they work.
Key features of custom brackets include:
- Bond Strength: Measured at 17.96 ± 2.01 MPa for 3D-printed ones.
- Retention: Improved by special design features.
- Durability: Just as reliable as regular brackets.
When choosing materials, think about what the bracket will be used for. Industrial brackets may need to be stronger, while commercial ones might focus on looking nice.
Material Selection for Indoor and Outdoor Applications
Picking the right material for indoor or outdoor use is important. Indoor brackets should use materials that don’t release harmful chemicals. Outdoor brackets need to resist water to avoid rust and mold.
Comparison of Indoor and Outdoor Material Criteria:
Criteria | Description |
---|---|
Indoor Air Quality | Use materials with low chemical emissions for cleaner air. |
Maintenance | Easy-to-clean materials last longer. |
Moisture Resistance | Outdoor materials should resist water to avoid rust and mold. |
For outdoor use, stainless steel and aluminum are great because they resist rust. Indoor brackets often use steel or custom brackets with coatings to look better and last longer.
By knowing how materials perform, you can pick the best one for your needs. Whether for industrial or commercial use, the right material makes brackets strong and long-lasting.
Metal Bracket Manufacturing Processes

Cutting and Shaping Techniques
Cutting and shaping are the first steps to make brackets. These steps decide the size and shape of the bracket. Tools like lasers, waterjets, or CNC machines are used. Laser cutting is fast and very accurate for detailed designs. Waterjet cutting uses strong water and grit to cut metal. This method avoids heat, keeping the metal’s properties safe. CNC machines shape metal automatically, making them great for large batches.
How well cutting works depends on the tools used. Tracking things like downtime and repairs can help improve processes. For example:
Metric | What It Measures |
---|---|
Overall Equipment Effectiveness | Shows how well machines are used, spotting problems in speed, quality, or availability. |
Downtime | Tracks when machines stop working, helping fix delays. |
Maintenance Metrics | Uses real-time data to predict and stop machine breakdowns. |
Quality KPIs | Checks for mistakes to lower waste and improve production. |
Watching these numbers helps keep cutting and shaping smooth and reliable.
Joining Methods in Metal Bracket Manufacturing
Joining connects metal parts to make strong brackets. Welding is often used for steel and aluminum brackets. It makes tough bonds but needs careful heat control. Automated methods, like hybrid metal-plastic joins, are lighter and work better. These methods skip glue or screws, saving time and weight.
Each joining method has good points and challenges:
Joining Method | Benefits | Challenges |
---|---|---|
Welding Aluminum to Steel | Combines different materials for strength. | Needs high heat; metals melt differently; can become brittle. |
Automated Joining of Hybrid Metal-Thermoplastic Composite Structures | Lighter and stronger joins without glue or screws. | Hard to bond metal and plastic; screws can harm fibers; glue adds weight. |
Knowing these details helps pick the best way to join parts.
Finishing Processes for Metal Sign Brackets
Finishing makes brackets look better and last longer. Methods like powder coating, anodizing, and polishing protect the surface. Powder coating adds a tough layer that stops rust and scratches. Anodizing makes aluminum stronger and adds color. Polishing smooths the surface, making it shiny for commercial use.
Checking the surface ensures the finish is good. Tests for coating thickness and stickiness check durability. By focusing on finishing, you can make brackets that look great and stay strong.
Design Considerations for Custom Metal Brackets
Strength and Load Capacity
Custom brackets must hold the weight they are designed for. The material’s strength is very important. Stainless steel is very strong (520 MPa) and resists rust, making it great for heavy jobs. Aluminum is lighter but still strong (310 MPa), good for medium loads.
Material | Tensile Strength (MPa) | Yield Strength (MPa) | Rust Resistance |
---|---|---|---|
Cold Rolled Steel | 420 | 250 | Moderate |
Stainless Steel 304 | 520 | 210 | Excellent |
Aluminum 6061 | 310 | 275 | Good |
Engineers use tools like FEA to test strength. This tool shows how brackets handle weight and pressure. For example, a bracket holding 200kg with 250 MPa strength needs at least 0.08 m² of material, including safety margins.
Style and Custom Options
Custom brackets can be made to fit your needs. You can pick finishes, shapes, and sizes for your project. CAD software helps design detailed 3D models. 3D printing allows for unique designs, like adjustable width or thickness.
These options make brackets useful for many purposes. You can choose shiny finishes for decoration or tough designs for heavy work. Customization ensures the brackets work well and look good.
Weather and Environmental Protection
The environment affects how brackets perform. For outdoor use, stainless steel and aluminum are great because they resist rust. Stainless steel can handle rain and humidity without damage.
Indoor brackets should use materials that are easy to clean and safe. Coatings like powder finishes add extra protection. They help brackets last longer and resist moisture. Picking the right material and finish keeps brackets strong and looking nice in any setting.
Quality Control in Metal Bracket Manufacturing
Making sure metal brackets are strong and reliable starts with good quality checks. Careful testing and inspections help find problems early. This keeps the manufacturing process at a high standard. Below are key ways to ensure metal sign brackets work well.
Inspection and Testing Methods
Testing and inspecting are important for quality control. These steps check if brackets match designs and work as needed. Visual checks find surface flaws, while measurements confirm size and alignment.
One method is sample inspection, where a few brackets from a batch are tested. For example, 50 brackets might be checked from a group of 5,000. If issues are found, a full inspection trigger means all brackets in the batch are tested. This saves time but keeps quality high. Another method, acceptance sampling, uses math to decide if a batch is good. A zero-acceptance plan ensures no bad brackets pass.
Following ISO 9000 rules helps keep processes consistent. These rules make sure written steps meet industry standards. Also, tools used for measuring must be properly calibrated for accurate results.
Quality Control Process | Description |
---|---|
Sample Inspection | A small number of brackets are tested from a batch. Example: 50 out of 5,000. |
Full Inspection Trigger | If a sample has defects, the whole batch is checked. |
Acceptance Sampling | Uses math to decide if a batch meets quality standards. |
ISO 9000 Compliance | Ensures processes follow industry-approved rules. |
Measurement Assurance | Tools are calibrated to ensure accurate measurements. |
Using these methods ensures every bracket meets top quality standards.
Non-Destructive Testing Techniques
Non-destructive testing (NDT) checks brackets for hidden problems without damaging them. These tests find cracks or flaws that could weaken the bracket. Common NDT methods include ultrasonic testing, X-rays, and magnetic particle testing.
- Ultrasonic Testing: High-frequency sound waves find cracks inside thick materials.
- X-ray Inspection: X-rays show internal flaws like holes or trapped particles.
- Magnetic Particle Testing: Finds surface cracks in magnetic metals like steel.
These tests help ensure brackets are safe and strong without harming them.
Mechanical Testing Standards
Mechanical tests check how strong and durable brackets are. These tests make sure brackets can handle the weight and stress they will face. ASTM standards guide these tests:
ASTM Standard | Description |
---|---|
ASTM E8/E8M | Tests how much force a bracket can take before breaking. |
ASTM A370 | Checks steel brackets for strength, bending, and hardness. |
ASTM E18 | Measures how hard the metal is to ensure durability. |
ASTM E23 | Tests how well brackets handle sudden impacts. |
ASTM E10 | Checks hardness in metals with rough textures. |
For example, tension tests (ASTM E8/E8M) measure how much force a bracket can take before it bends or breaks. Hardness tests (ASTM E18) check how tough the metal is. Impact tests (ASTM E23) see if brackets can handle sudden hits without breaking.
By following these standards, you can make sure your brackets are strong and ready for their jobs.
Surface and Coating Quality Checks
Surface and coating checks help metal brackets last longer. These steps improve how brackets look and protect them from damage. They also make brackets stronger and less likely to wear out.
Why Surface Quality Matters
The surface finish affects how well brackets work. Smooth surfaces lower stress and prevent cracks. For example, machining Ti-6Al-4V metal can make it last four times longer. This happens because smoother surfaces stop cracks from forming under pressure. But hidden pores inside metals like SLM Ti64 can weaken them. These pores make surface quality even more important.
Ways to Coat Metal Brackets
Coatings keep brackets safe from damage. Powder coating adds a tough layer that stops rust and scratches. Anodizing makes aluminum stronger and adds color choices. Ultrasonic cavitation abrasive finishing (UCAF) smooths surfaces but works best on already clean surfaces.
Coating Type | Benefits | Challenges |
---|---|---|
Powder Coating | Stops rust and scratches. | Needs careful application. |
Anodizing | Strengthens aluminum; adds color. | Only works on aluminum. |
UCAF | Smooths rough surfaces. | Works better on clean surfaces. |
How Quality Checks Help
Quality checks make sure coatings and surfaces meet high standards. Tests measure how thick and sticky coatings are. These tests show if the protective layer will last in tough conditions. Smoother surfaces also help brackets handle stress better. By focusing on these details, brackets can be strong and look great.
Fixing Problems in Metal Sign Brackets
Issues Found in Metal Brackets
Problems in metal brackets can make them weaker or less useful. Common issues include cracks, bending, or tiny holes called porosity. Cracks happen during welding or when too much pressure is applied. Bending occurs if the metal heats or cools unevenly, changing its shape. Porosity creates small holes that make the bracket less strong and able to hold weight.
Scratches or uneven coatings can also harm how the bracket looks and works. These flaws might cause rust or damage, especially outside. Finding these problems early helps ensure the brackets are strong and meet quality standards.
How to Stop Problems During Manufacturing
Stopping problems starts with good planning and careful work. Use clean, high-quality materials to avoid impurities. During welding, control the heat and use proper methods to stop cracks. Heating the metal before welding and cooling it evenly can prevent bending.
Keeping machines in good condition is also important. Tools for cutting, shaping, and finishing need to work well to avoid mistakes. Checking for problems at every step of production helps catch issues early. For example, ultrasonic testing can find hidden holes inside the metal. These steps help lower mistakes and make better brackets.
Fixing and Checking After Problems Are Found
Fixing problems quickly keeps brackets working well. Welding can repair cracks, and grinding smooths out rough spots. Filling holes caused by porosity with matching materials makes the bracket strong again.
After fixing, check the brackets carefully to ensure repairs are good. Non-destructive tests, like X-rays, can confirm the bracket is safe and strong. Adding surface coatings, such as powder finishes, improves how the bracket looks and protects it from damage. These steps make sure repaired brackets are reliable and ready to use.
Keeping Production Consistent
Controlling Processes and Following Standards
To keep production consistent, you need strict controls. Follow clear rules and check important performance numbers. For example:
- Accuracy: Makes sure every bracket is made the same way.
- Efficiency: Measures how fast and smooth production runs.
Some industries, like car-making, need very precise brackets. They use tolerances as small as ±0.1mm to ensure perfect fits. Injection molding helps keep quality steady by using strict checks. Watching these numbers reduces mistakes and makes strong brackets in large amounts.
Using Automation for Better Manufacturing
Automation helps make brackets faster and more accurate. Tools like robots, CNC machines, and smart devices improve production. For example:
Technology | What It Does | How It Helps |
---|---|---|
Robots | Handle repeated tasks without mistakes. | Safer work and better product quality. |
CNC Machines | Cut and shape metal with high accuracy. | Makes parts more precise. |
Robots can weld metal perfectly every time. Robotic arms move materials quickly and safely. Smart devices track production in real time, helping fix problems fast. Automated systems also check for flaws, ensuring every bracket is perfect. These tools save time, reduce waste, and improve quality.
Using Data and Quality Systems
Data and quality systems help keep production at a high level. Statistical Process Control (SPC) uses numbers to spot problems early. For example, checking bracket sizes ensures they stay within limits.
Quality Management Systems (QMS), like ISO 9001, set rules for steady production. They focus on keeping records, doing regular checks, and improving processes. Using SPC and QMS together creates a strong system. This system ensures reliable brackets, builds customer trust, and boosts your reputation for great products.
Supplier Qualification and Material Traceability
Picking good suppliers is key for making strong metal brackets. Suppliers must provide high-quality materials that match your needs. To check suppliers, look at their certifications, skills, and if they follow industry rules. For example, ISO 9001 shows they use good quality systems.
Tracking materials is also very important. It helps you know where the materials came from and how they were made. This ensures every batch meets your standards and follows rules. Traceability systems save details like material type, batch number, and date made. These records help find and fix problems fast if something goes wrong.
Tip: Always ask suppliers for material certifications. These papers prove the materials’ chemical makeup and strength.
To qualify a supplier, follow these steps:
- Check Certifications: Look at their records and past work.
- Visit Their Facility: See their tools and how they work.
- Test Order: Buy a small amount to check material quality.
Traceability tools like barcodes or RFID tags track materials during production. These tools help manage inventory and follow rules. For example, if a batch fails a test, you can trace the problem back to the material lot and supplier.
By choosing reliable suppliers and tracking materials, you can keep your brackets high-quality. These steps lower risks, improve trust, and make your products dependable.
Picking good materials helps make strong and useful brackets. Knowing the types of metal brackets ensures they work well and last long. Careful manufacturing and smart designs make brackets sturdy and nice-looking. Checking for quality helps find and fix problems early.
Quality checks make sure brackets handle tough conditions indoors or outdoors. If you need special brackets for your needs, ask experts for help. They can guide you to create brackets that are strong and look great.
At OPTRAFFIC, we prioritize quality assurance in every step of the manufacturing process, ensuring our road sign brackets for sale meet the highest standards for durability and performance. Learn more about our commitment to quality here.
FAQ
What materials are often used for metal sign brackets?
Steel, aluminum, and stainless steel are common choices. Steel is strong, aluminum is light and doesn’t rust, and stainless steel is tough and resists corrosion.
How is the quality of metal sign brackets checked?
Manufacturers test brackets using inspections and special tools. These tests look for cracks, strength, and surface flaws. Following rules like ISO 9001 keeps quality steady.
Can metal sign brackets be made to fit specific needs?
Yes, you can pick materials, finishes, and designs for custom brackets. Coatings like powder or anodizing make them stronger and better-looking. CAD software helps design brackets to match your needs.
How can rust be stopped on outdoor brackets?
Use materials like stainless steel or aluminum that resist rust. Protective coatings, such as powder finishes, add extra defense against water and weather.
Why is tracking materials important in manufacturing?
Tracking shows where materials come from and how they’re used. It ensures good quality, finds problems fast, and follows industry rules. This builds trust in the final product.