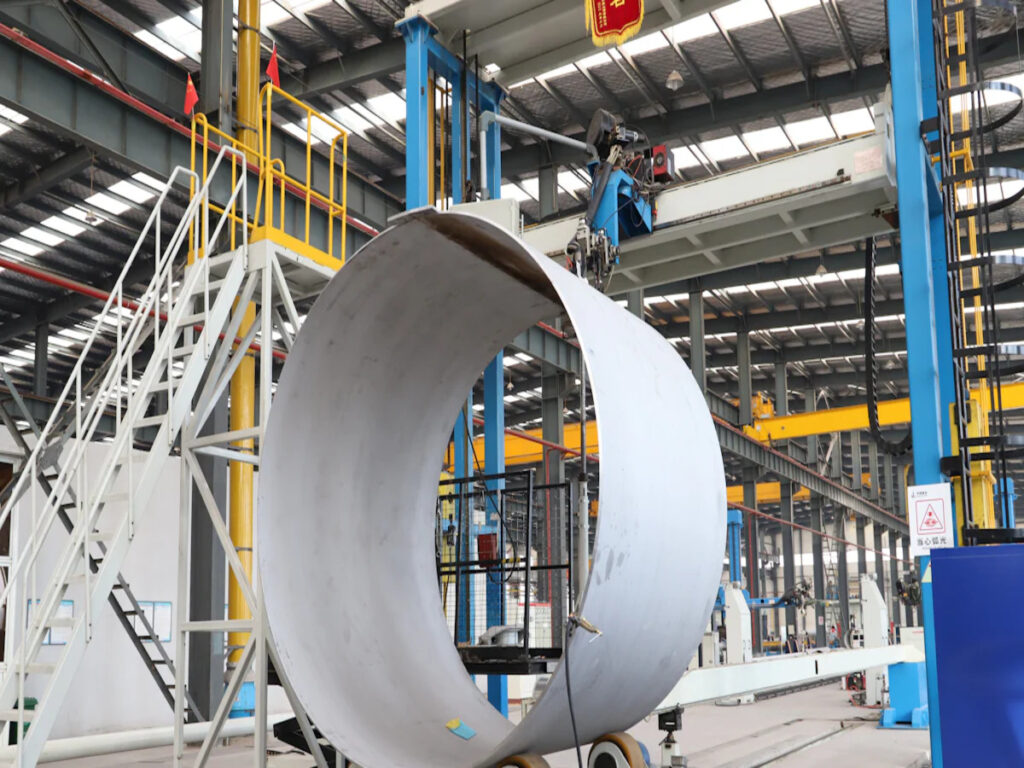
Understanding how work cones are manufactured helps you appreciate their quality and performance. The materials used play a critical role in determining their durability and cost-effectiveness. Manufacturers face challenges like sourcing materials that meet strength and heat resistance requirements. They also need to ensure structural integrity and stress resistance to handle extreme conditions. Customizing designs for specific needs adds complexity to the process. Innovations in production methods aim to improve quality while reducing costs, addressing these challenges effectively. By learning about these processes, you can better understand the effort behind creating reliable work cones.
Injection Molding for Work Cones
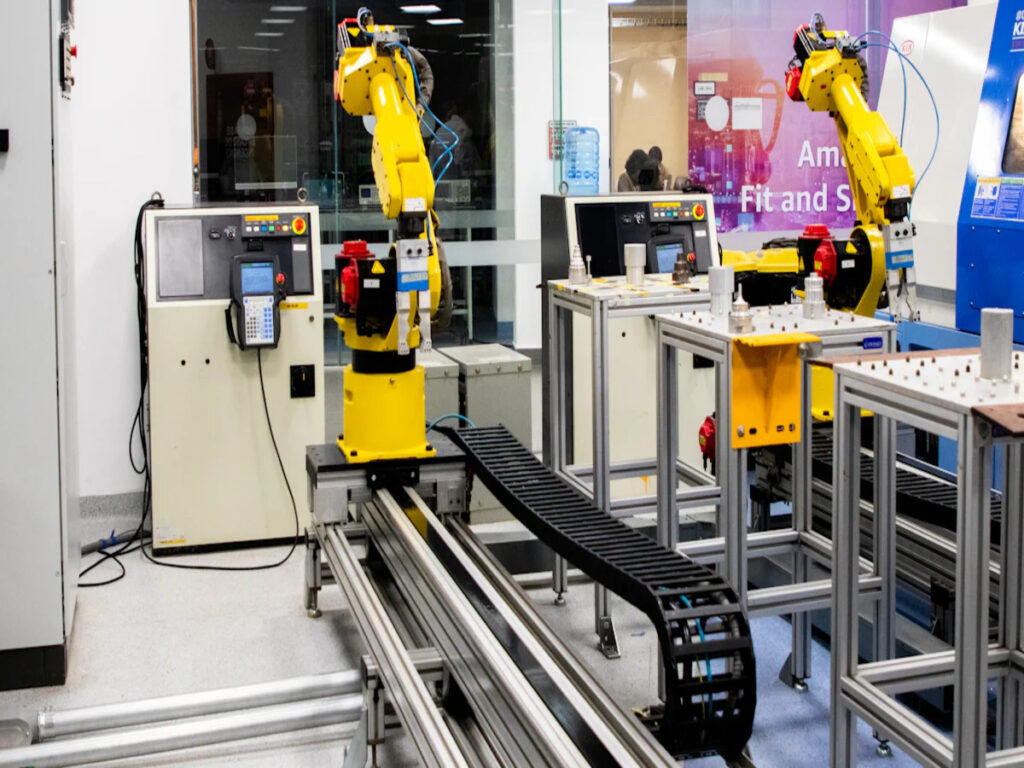
Process Description
How Injection Molding Works
Injection molding is a widely used process for creating durable and precise work cones. It begins with the preparation of raw materials. You inspect and measure the materials to ensure they meet the required specifications. If inserts are needed, you prepare them during this stage. The next step involves feeding the raw material into the injection molding machine. The material is heated until it becomes a viscous fluid, a process known as plasticization. Once the material reaches the right consistency, it is injected into a mold cavity. The mold shapes the material into the desired cone structure as it cools and solidifies.
Equipment Used in Injection Molding
The equipment for injection molding includes an injection molding machine, molds, and auxiliary tools. The machine consists of a hopper, a heating barrel, and an injection unit. The hopper holds the raw material, while the heating barrel melts it. The injection unit pushes the molten material into the mold cavity. Molds are typically made of steel or aluminum and are designed to create the specific shape of the cones. Auxiliary tools, such as temperature controllers and cooling systems, ensure the process runs smoothly and efficiently.
Application to Work Cones
Benefits of Injection Molding
Injection molding offers several advantages when manufacturing work cones. It allows for high precision, ensuring each cone meets exact specifications. The process is highly efficient, enabling mass production at a lower cost per unit. It also supports the use of various materials, allowing you to choose options that enhance durability and performance. Además, injection molding minimizes waste, making it an environmentally friendly choice.
OPTsign traffic cones are manufactured using advanced injection molding technology, ensuring precise, consistent quality in every unit.
Limitations of Injection Molding
Despite its benefits, injection molding has some challenges. Managing the design and maintenance of molds can be complex and time-consuming. Errors in mold design may lead to defects in the final product. Estimating the right amount of raw material can also be tricky, potentially causing shortages or excesses. Equipment maintenance is another critical factor. Downtime due to equipment failure can disrupt production and increase costs.
Blow Molding for Road Cones
Process Description
How Blow Molding Works
Blow molding is a manufacturing process designed to create hollow plastic products. It begins with heating a plastic material, typically in the form of a tube or parison, until it becomes soft and pliable. Once heated, you place the parison into a mold. Air is then blown into the tube, inflating it to match the shape of the mold cavity. After cooling, the mold opens, and the finished product is ejected. This process is ideal for producing lightweight and hollow items, such as road cones.
Equipment Used in Blow Molding
The equipment for blow molding includes an extruder, a mold, and an air compressor. The extruder melts and shapes the plastic into a parison. The mold, usually made of metal, determines the final shape of the product. The air compressor provides the necessary pressure to inflate the plastic. Additional tools, such as cooling systems, ensure the product solidifies quickly and maintains its shape.
Application to Road Cones
Benefits of Blow Molding
Blow molding offers several advantages when manufacturing road cones. The process is highly cost-efficient due to its low material usage and minimal maintenance requirements. It also operates at high speeds, allowing you to produce large quantities quickly. Automated systems ensure consistent quality, reducing errors and waste. Además, blow molding supports the use of recyclable plastics like HDPE, making it an environmentally friendly option.
Limitations of Blow Molding
Despite its benefits, blow molding has limitations. The process is best suited for simpler designs, as it cannot achieve the intricate details possible with injection molding. Wall thickness may vary, which can affect the durability of the cones. The initial setup cost for molds and equipment can also be high, making it less suitable for small production runs.
Compression Molding for Work Cones
Process Description
How Compression Molding Works
Compression molding is a straightforward yet effective manufacturing process. It begins with placing a pre-measured amount of material, often in the form of a solid or semi-solid, into a heated mold cavity. You then close the mold using a hydraulic press, applying heat and pressure to shape the material into the desired form. The heat activates the material, causing it to flow and fill the mold cavity completely. Once the material cures and solidifies, you open the mold and remove the finished cone. This process works well for creating durable and heat-resistant products.
Equipment Used in Compression Molding
The equipment for compression molding includes a hydraulic press, molds, and heating systems. The hydraulic press applies the necessary pressure to shape the material. Molds, typically made from steel or aluminum, determine the final shape of the cones. Heating systems ensure the material reaches the required temperature for proper curing. Additional tools, such as trimming devices, help remove excess material after the molding process.
Application to Work Cones
Benefits of Compression Molding
Compression molding offers several advantages for manufacturing work cones. It is highly versatile, allowing you to use a wide range of materials, incluido thermosetting plastics. The process produces strong and durable traffic cones that can withstand harsh conditions. It is also cost-effective for medium to large production runs, as the molds are relatively simple and inexpensive to produce. Además, compression molding generates minimal waste, making it an environmentally friendly option.
Limitations of Compression Molding
Despite its benefits, compression molding has some drawbacks.
- Longer cycle times slow down production rates, making it less efficient for high-volume manufacturing.
- Manual handling and frequent mold maintenance increase labor costs.
- Achieving high precision and tight tolerances is challenging, limiting its use for intricate designs.
- Excess material, known as flash, often forms at the mold’s parting line and requires post-processing.
- Material choices are limited compared to other methods, as the process primarily suits thermosetting plastics.
- Longer setup times reduce efficiency, especially for short production runs.
By understanding these limitations, you can determine if compression molding aligns with your specific manufacturing needs.
Metal Cone Fabrication
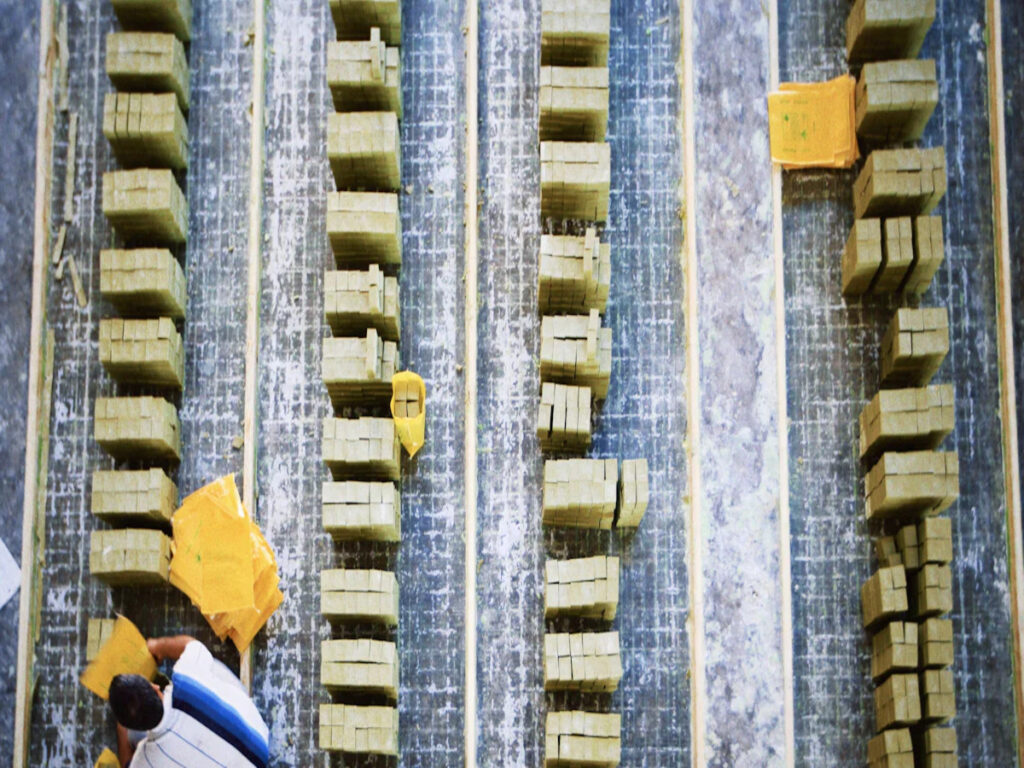
Process Description
Rolling and Press Braking
Rolling and press braking are essential techniques in the process of metal cone fabrication. Rolling involves passing a flat metal sheet through a series of rollers to gradually form it into a conical shape. This method is ideal for creating symmetrical cones with consistent dimensions. Press braking, por otro lado, allows you to form more complex shapes, such as eccentric or asymmetrical cones. This process uses a press brake machine to bend the material incrementally in sections, achieving the desired radius. These techniques are particularly useful when precision and durability are critical in manufacturing.
Metal Spinning Techniques
Metal spinning is another effective process for fabricating cones. This technique uses a lathe or a cylindrical mandrel to shape a flat metal sheet into a seamless conical structure. The spinning process involves applying pressure to the material while it rotates, ensuring uniformity and strength. Metal spinning is highly efficient and versatile, making it suitable for both simple and intricate designs. It also adapts well to modern manufacturing needs, offering precision and cost savings.
Application to Work Cones
Benefits of Metal Cone Fabrication
Metal cone fabrication offers several advantages. Metal spinning, por ejemplo, provides flexibility in creating various shapes and sizes. It allows you to produce intricate, symmetrical, and seamless structures. The tooling costs are relatively low, making it an economical choice for quick production. Además, rolling and press braking ensure high precision and durability, which are essential for work cones used in demanding environments.
Limitations of Metal Cone Fabrication
Despite its benefits, metal cone fabrication has some limitations. Rolling and press braking may require specialized equipment and skilled operators, increasing initial costs. Metal spinning, while efficient, may not be suitable for extremely large-scale production due to its manual nature. Además, the process may generate waste material, which could impact overall efficiency.
Comparison of Manufacturing Methods
Advantages of Each Method
Each manufacturing method offers unique benefits depending on the production process and the type of cones you need.
- Injection molding provides high precision and is ideal for complex designs. Its automated systems ensure consistent quality, making it perfect for large-scale production.
- Blow molding excels in creating lightweight and hollow structures, such as road cones. This process operates efficiently and uses recyclable materials, which makes it environmentally friendly.
- Compression molding works well for larger parts and is cost-effective for medium production volumes. It uses simpler equipment, which reduces initial setup costs.
- Metal fabrication, including rolling and spinning, produces durable and seamless cones. This method is highly versatile, allowing you to create intricate shapes with low tooling costs.
Limitations of Each Method
While each process has strengths, you should also consider their limitations.
- Injection molding requires significant upfront investment in molds and equipment. It may not be cost-effective for small production runs.
- Blow molding struggles with intricate designs and may produce cones with inconsistent wall thickness. This can affect durability.
- Compression molding has longer cycle times, which slows down production. It also generates excess material, requiring additional post-processing.
- Metal fabrication demands skilled operators and specialized equipment. It may not suit high-volume production due to its manual nature.
Choosing the Right Method for Specific Needs
Selecting the best production process depends on your specific requirements. For high-volume needs, injection molding offers speed and precision. OPTsigns leverage this technology to deliver high-quality, consistent traffic cones that meet the demands of safety and durability, ensuring reliable performance for every project. If you need lightweight and hollow cones, blow molding is the better choice. Compression molding suits medium-scale production and larger parts. For durable and intricate designs, metal fabrication provides unmatched versatility. Consider factors like cost, material, and design complexity to make the right decision.
Consejo: Evaluate your production goals and budget before choosing a method. This ensures you achieve the best balance between quality and efficiency.
You’ve explored various manufacturing methods for work cones, each offering unique advantages and limitations. Choosing the right method depends on your specific needs, including cost, durabilidad, and application. Por ejemplo, custom moulding techniques like injection or compression moulding provide precision and efficiency, while metal fabrication ensures durability for demanding environments.
Innovation plays a vital role in improving sustainability. Energy-efficient processes reduce pollution and carbon emissions. Using renewable materials and sustainable alternatives supports recycling and minimizes waste. Modular traffic cone designs also conserve resources and reduce environmental impact. These advancements not only enhance recyclability but also protect the environment from microplastics and other pollutants.
By prioritizing sustainable practices, Contribuyes a un futuro más verde.. Whether producing traffic barriers or cones, adopting green alternatives ensures long-term benefits for both the environment and manufacturing efficiency.