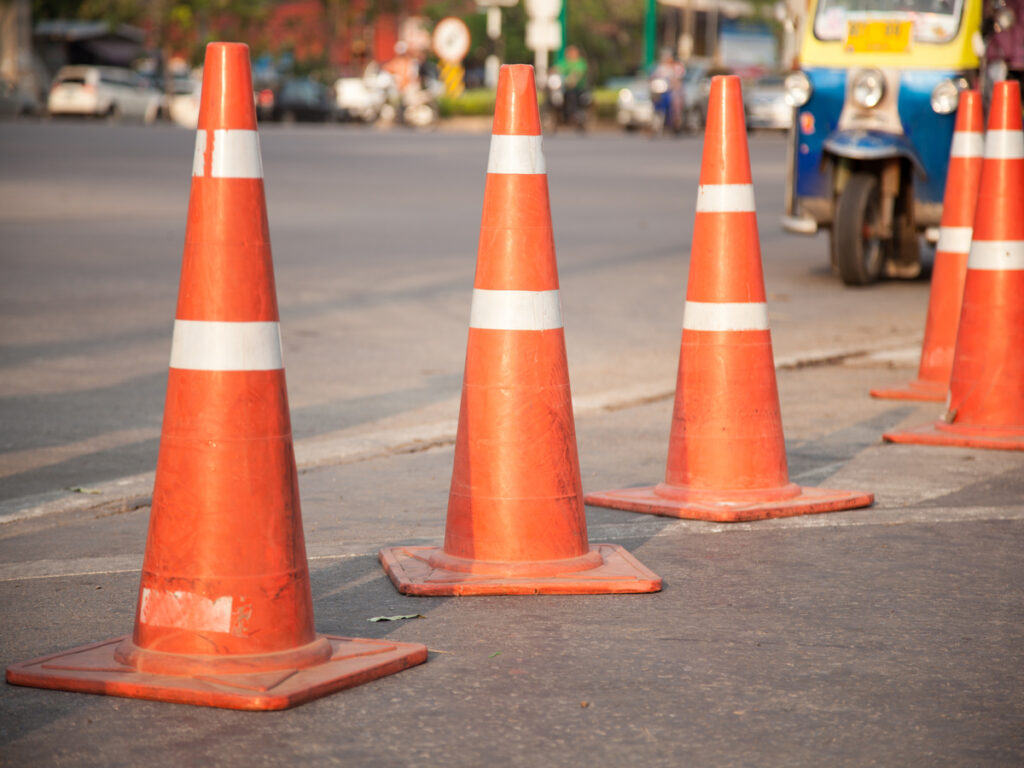
Traffic cones play a vital role in keeping roads safe and organized. You’ve likely seen them guiding drivers through construction zones or marking off restricted areas. Their bright colors and strategic placement grab attention, reducing the risk of accidents. Choosing the right traffic cone matters too. Taller traffic cones improve visibility, while heavier ones stay stable in windy conditions. Misplaced cones, however, can lead to tragic outcomes, as seen in cases where poor placement caused severe accidents. Understanding the different types of traffic cones and their proper use ensures safety for everyone on the road.
Overview of Traffic Cone Regulations and Standards
Traffic cones might seem simple, but they follow strict rules to ensure they do their job effectively. These rules, outlined in the Manual on Uniform Traffic Control Devices (MUTCD), set the standard for how cones should look and where they should go. Let’s dive into the details.
If you’d like to know more about traffic cones and products, you can visit OPTsigns. We offer a variety of traffic cones that meet all regulatory standards.
The MUTCD and Its Role in Traffic Cone Guidelines
The MUTCD serves as the ultimate guide for all traffic control devices, including traffic cones. It ensures consistency across the country, so whether you’re driving in California or New York, you’ll encounter cones that meet the same standards. According to the MUTCD, cones must be predominantly orange to grab attention. Their material should be flexible enough to avoid damage if struck by a vehicle.
Height requirements also vary based on the situation. For daytime use on low-speed roads, cones must be at least 18 inches tall. On freeways, high-speed highways, or during nighttime, types of traffic cones must stand at least 28 inches tall. These guidelines ensure types of traffic cones remain visible and effective, even in challenging conditions.
“Traffic control devices, including cones, must command attention, convey a clear meaning, command respect from road users, and provide adequate time for proper response.” – Federal Highway Administration
By following these rules, cones help maintain order and safety on roads and worksites.
Key Features of Traffic Cones: Size, Color, and Reflectivity
Not all traffic cones are created equal. Their size, color, and reflectivity play a big role in how well they perform. The bright orange color isn’t just for looks—it’s a universal signal for caution. This color ensures drivers and pedestrians notice the cones immediately, reducing the risk of accidents.
Reflective bands are another critical feature. These bands make cones visible at night or in low-light conditions. The MUTCD requires cones used on high-speed roads or at night to have reflective materials. This ensures they remain effective, even when visibility is poor.
Size matters too. Taller cones are easier to spot from a distance, especially on busy highways. Heavier cones stay in place during windy weather or when vehicles pass by at high speeds. Choosing the right traffic cone for the right scenario ensures maximum effectiveness.
General Placement and Spacing Rules for Traffic Cones
Placing traffic cones isn’t just about dropping them randomly. Proper placement follows specific rules to guide traffic and keep everyone safe. The MUTCD recommends placing cones in a taper formation to direct vehicles smoothly. For example, when closing a lane, cones should gradually guide drivers into the open lane.
Spacing between cones depends on the speed of traffic. On low-speed roads, cones can be closer together. On highways, they need to be spaced farther apart to give drivers enough time to react. These spacing rules ensure cones communicate clear instructions without causing confusion.
When setting up cones, always think about visibility. Make sure they’re easy to see from a distance and aren’t blocked by other objects. Proper placement not only improves safety but also keeps traffic flowing smoothly.
Traffic Cone Requirements in Different Scenarios
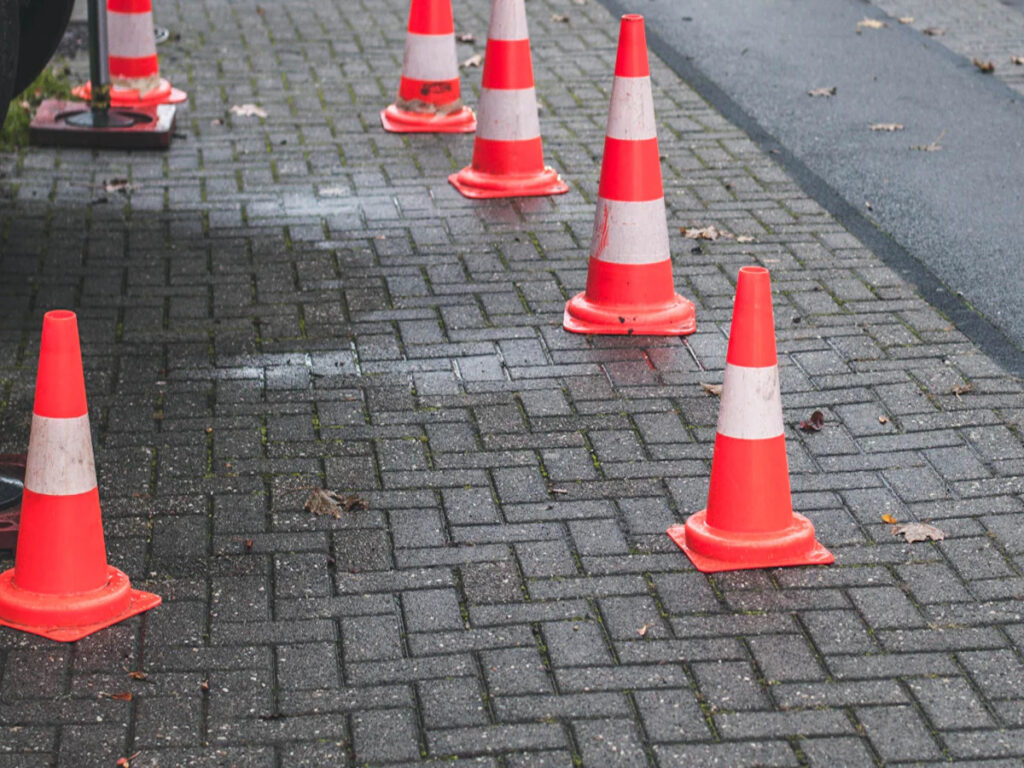
Work Zones
Work zones demand careful planning and execution to ensure safety for both workers and drivers. Traffic cones play a crucial role in creating a clear and organized environment, minimizing risks and maintaining smooth traffic flow.
Lane Closures and Taper Lengths
When closing a lane in a work zone, you need to use traffic cones strategically to guide vehicles safely. The MUTCD emphasizes the importance of taper lengths, which depend on the speed of traffic and the width of the lane. For example, on high-speed roads, longer tapers provide drivers with more time to adjust. Cones should be placed in a gradual line to create a smooth transition, reducing confusion and potential hazards.
Proper spacing between cones is also essential. On highways, cones are spaced farther apart to give drivers enough time to react. On low-speed roads, closer spacing ensures better guidance. This thoughtful placement enhances visibility and keeps the work zone safe.
Delineating Work Areas for Worker Safety
Protecting workers in a work zone requires clear boundaries. Traffic cones act as channelizing devices, separating work areas from active traffic lanes. This separation reduces the risk of accidents and ensures workers can focus on their tasks without constant worry.
To maximize protection, traffic cones should be tall enough to remain visible from a distance. Heavier cones are ideal for windy conditions or areas with high-speed traffic. By following these guidelines, you create a safer environment for everyone involved.
Data Analysis
Data helps determine the number of cones needed for a work zone. For every 100 meters of road work, the quantity of traffic cones depends on factors like road width, traffic flow, and construction scale. For instance, a large-scale road reconstruction project may require hundreds of traffic cones to manage traffic diversion effectively. Using data ensures your traffic management plan is both efficient and compliant with OSHA and MUTCD standards.
Pedestrian Areas
Pedestrian areas require a different approach to traffic cone usage. Here, the focus shifts to guiding foot traffic and ensuring accessibility for all individuals.
Creating Safe Walkways and Detours
In pedestrian zones, traffic cones help create temporary walkways and detours. These pathways keep pedestrians away from hazards like construction sites or road work. Bright orange cones grab attention, while reflective bands ensure visibility in low-light conditions. By marking clear routes, you reduce confusion and enhance safety for pedestrians.
Ensuring Accessibility Compliance
Accessibility compliance is vital in pedestrian areas. Cones should guide individuals, including those with disabilities, through safe and accessible routes. For example, cones can mark ramps or detours that accommodate wheelchairs. Following these practices ensures your traffic control layout meets legal requirements and prioritizes inclusivity.
Data Analysis
Estimating cone requirements for pedestrian areas involves analyzing foot traffic and the size of the zone. For instance, a busy city sidewalk may need more cones to manage high pedestrian flow. Data-driven decisions improve the effectiveness of your traffic management plan, ensuring smooth movement and safety. Generally, place one traffic cone every 5 to 10 meters to clearly mark the boundaries, guide pedestrian flow, or create a barrier for safety.
Road Closures and Detours
Road closures and detours present unique challenges. Traffic cones become essential tools for guiding vehicles and maintaining order during these situations.
Marking Detour Routes
When closing a road, you must provide clear detour routes. Cones mark these routes, ensuring drivers know where to go. The MUTCD recommends using cones in combination with advance warning signs to prepare drivers for upcoming changes. This combination minimizes confusion and keeps traffic moving efficiently.
Managing Traffic Flow Around Closed Areas
Managing traffic flow around closed areas requires strategic cone placement. Cones should direct vehicles smoothly, avoiding sudden stops or sharp turns. Proper spacing and alignment improve visibility and reduce the risk of accidents. By following these practices, you maintain order and protect drivers from potential hazards.
Data Analysis
Data analysis helps determine the number of cones needed for road closures. Factors like the length of the closure and the volume of traffic influence this number. For example, a short-term closure on a low-traffic road may need fewer cones than a long-term closure on a busy highway. Using data ensures your traffic control layout is both effective and resource-efficient.
Parking Lots and Public Facilities
Estimating Cone Requirements Based on Parking Spaces
Parking lots require a well-thought-out traffic management plan to ensure smooth vehicle movement and pedestrian safety. Traffic cones play a key role in organizing these spaces effectively. To estimate the number of cones needed, consider the size of the parking lot and the number of parking spaces. For instance, larger lots with multiple entrances may need more cones to guide vehicles and mark restricted areas.
You should also think about visibility. Taller traffic cones work best in expansive parking areas, as they are easier to spot from a distance. Heavier cones provide stability, especially in outdoor lots where wind can be an issue. By choosing the right types of traffic cones, you can create a layout that ensures order and safety for all users.
Emergency Parking and Temporary Event Management
Temporary events and emergency situations demand quick and efficient traffic control. Traffic cones help you create temporary parking zones or redirect vehicles during emergencies. For example, during a large event, cones can mark designated parking areas, ensuring attendees park in an organized manner.
In emergencies, cones guide vehicles to safe zones or mark off restricted areas. The MUTCD recommends using reflective cones for nighttime or low-light conditions to maintain visibility. Proper cone placement ensures smooth traffic flow and minimizes confusion during high-pressure situations. By planning ahead, you can use cones to manage these scenarios effectively.
Data Analysis
Data plays a crucial role in determining cone requirements for parking lots and public facilities. Factors like the number of parking spaces, entrances, and expected traffic volume influence the quantity of cones needed. For example, a supermarket parking lot with 200 spaces may require around 50 safety cones to manage entry and exit points, as well as pedestrian pathways. Using data ensures your traffic management plan is both efficient and compliant with MUTCD and OSHA standards.
Campus and School Safety Management
Ensuring Student Safety with Proper Cone Deployment
Schools and campuses require a unique approach to traffic management. Traffic cones help you create safe zones for students, especially during drop-off and pick-up times. You can use cones to separate pedestrian walkways from vehicle lanes, ensuring students move safely through the area.
For maximum protection, place cones at key points like crosswalks, entrances, and exits. Taller cones improve visibility for drivers, while reflective cones enhance safety during early morning or evening hours. By deploying cones strategically, you create a safer environment for students and staff.
Managing Traffic Flow During School Events
School events often bring increased traffic, making proper cone deployment essential. Cones help you manage vehicle flow, direct attendees to parking areas, and mark restricted zones. For example, during a sports event, cones can guide vehicles to designated parking lots and prevent congestion near the main entrance.
The MUTCD emphasizes the importance of clear and visible traffic control devices. Reflective cones ensure drivers can navigate safely, even in low-light conditions. By planning your cone layout carefully, you can maintain order and ensure a smooth experience for everyone.
Data Analysis
Analyzing data helps you determine the number of cones needed for school safety management. Factors like the size of the campus, the number of entrances, and the volume of traffic influence this number. For instance, a large high school with multiple parking lots may require over 100 cones to manage traffic effectively. Data-driven decisions ensure your traffic management plan meets safety standards and keeps everyone protected.
Traffic Accident Sites and Emergency Response
Standard Cone Requirements for Accident Management
Traffic cones are essential tools for managing accident sites. They help you create a safe perimeter around the scene, protecting both responders and drivers. The MUTCD recommends using at least 16 cones for emergency response vehicles to guide traffic into available lanes.
You should choose cones that are tall and reflective to ensure visibility, especially on high-speed roads or during nighttime. Proper cone placement reduces the risk of secondary accidents and keeps the scene organized.
Positioning Cones for Efficient Traffic Control
Positioning cones correctly is crucial for effective traffic control at accident sites. Place cones in a taper formation to guide vehicles smoothly around the scene. The MUTCD advises spacing cones farther apart on high-speed roads to give drivers enough time to react.
You should also consider the size of the area that needs to be cordoned off. Larger accident scenes may require more cones to ensure complete coverage. By following these guidelines, you can maintain order and protect everyone involved.
Data Analysis
Data helps you determine the number of safety cones needed for accident management. Factors like the size of the accident site, traffic volume, and road conditions influence this number. For example, a multi-vehicle accident on a busy highway may require over 50 safety cones to manage traffic diversion effectively. Using data ensures your traffic management plan is both efficient and compliant with MUTCD and OSHA standards.
In short, each use case requires a certain number of traffic cones. At OPTsigns, you can purchase a large quantity of traffic cones at affordable prices, don’t have to worry about cost.
The Power of Numbers: How Quantity and Placement Impact Safety
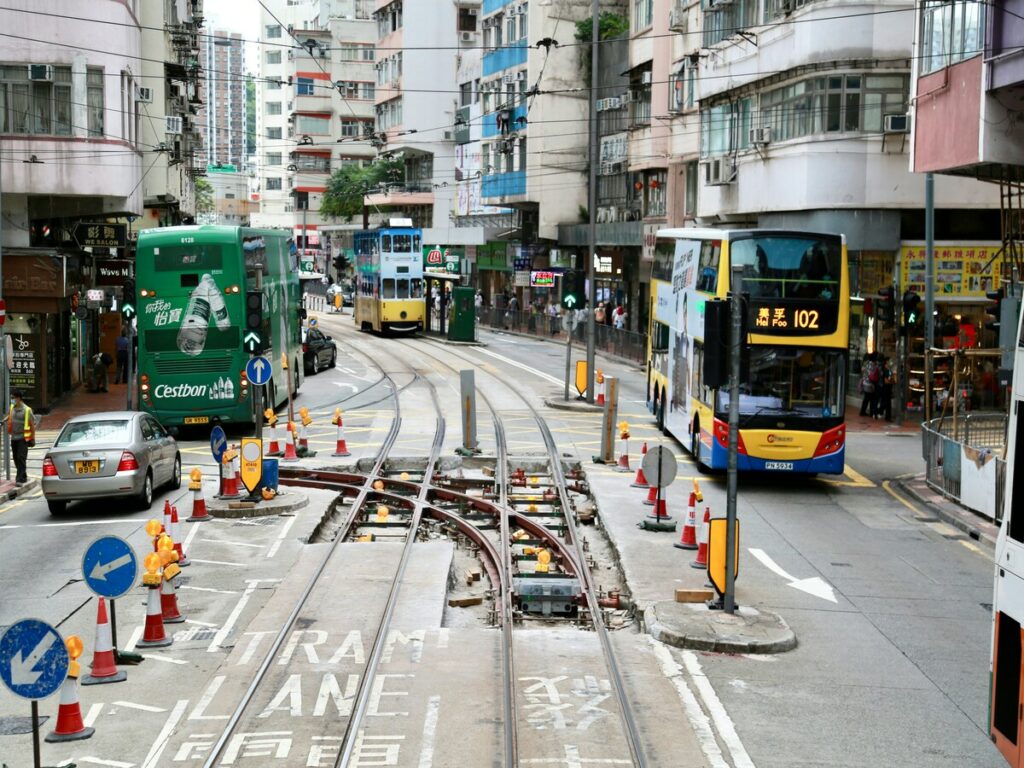
The Role of Cone Density in Traffic Flow Management
The density of traffic cones in a work zone directly affects how smoothly vehicles move through the area. When you place cones too far apart, drivers may not have enough guidance, leading to confusion or sudden stops. On the other hand, placing cones too close together can create unnecessary congestion. Striking the right balance is key to maintaining order and ensuring safety.
For example, on high-speed roads, cones should be spaced farther apart to give drivers ample time to react. In contrast, low-speed areas, like urban road work zones, benefit from closer cone placement to provide clear direction. The Manual on Uniform Traffic Control Devices (MUTCD) offers specific guidelines for spacing based on traffic speed and road conditions. By following these standards, you can create a traffic management plan that minimizes risks and keeps vehicles moving efficiently.
Strategic Placement for Maximum Visibility and Effectiveness
Strategic cone placement ensures that drivers and pedestrians notice them in time to respond appropriately. Visibility plays a huge role here. Taller cones, especially those over 28 inches, are ideal for highways and high-speed roads. Their height makes them easier to spot from a distance, giving drivers more time to adjust. Reflective collars further enhance visibility during nighttime or low-light conditions.
You should also consider the layout of the work zone. Cones placed in a taper formation guide vehicles smoothly into open lanes, reducing confusion. For pedestrian areas, cones can mark safe walkways and detours, keeping foot traffic away from hazards. Proper placement not only improves safety but also enhances the overall effectiveness of your traffic control measures.
“Adhere to Proper Cone Placement: Cone placement is critical to maintaining a secure work zone.” – Federal Highway Administration
By positioning cones thoughtfully, you ensure they serve their purpose effectively, whether on a busy highway or a quiet parking lot.
Balancing Cost and Safety: How Many Cones Are Enough?
Determining the right number of cones for a work zone involves balancing cost and safety. Using too few cones can compromise protection, while overusing them may inflate costs unnecessarily. Data analysis helps you find this balance. For instance, factors like road width, traffic volume, and the scale of the work zone influence the number of cones required.
On average, a 100-meter stretch of road work may need dozens of cones, depending on the complexity of the project. High-traffic areas or large-scale construction sites often require more cones to manage traffic effectively. Emergency response vehicles, as recommended by the MUTCD, should carry at least 16 cones to guide traffic safely during incidents. By analyzing these variables, you can create a cost-effective traffic management plan that doesn’t compromise safety.
Ultimately, the power of numbers lies in their ability to enhance safety and efficiency. Whether you’re managing a work zone, a parking lot, or a school campus, the right quantity and placement of cones make all the difference.
Best Practices for Setting Up Traffic Cones
Ensuring Visibility: Reflective Materials and Lighting
Visibility is the cornerstone of effective traffic cone usage. You want drivers and pedestrians to notice cones immediately, even in challenging conditions. Reflective materials play a significant role here. Cones with reflective bands catch light from vehicle headlights, making them visible during nighttime or in low-light environments. This feature ensures that cones remain effective regardless of the time of day.
Lighting also enhances visibility. In areas with poor lighting, you can use portable lights or illuminated cones to draw attention. These tools are especially useful in high-risk zones like highways or during emergency situations. By prioritizing visibility, you reduce the chances of accidents and improve overall safety.
“Strategic cone placement ensures maximum visibility and effectiveness, especially in high-speed or low-light conditions.” – Federal Highway Administration
When setting up cones, always consider the environment. Choose taller cones for highways and ensure reflective materials meet the standards outlined by OSHA and MUTCD. These small adjustments make a big difference in keeping everyone safe.
Proper Spacing and Alignment for Different Scenarios
Spacing and alignment are critical for creating an effective traffic management plan. Proper spacing ensures that cones guide drivers smoothly without causing confusion. On high-speed roads, cones should be spaced farther apart to give drivers enough time to react. In contrast, low-speed areas like urban road work zones benefit from closer spacing for better guidance.
Alignment also matters. Cones arranged in a taper formation help direct traffic into open lanes or around obstacles. This layout minimizes sudden stops and keeps traffic flowing efficiently. For pedestrian areas, align cones to create clear walkways and detours, ensuring safety for foot traffic.
When planning your cone setup, think about the type of road and the volume of traffic. Adjust spacing and alignment based on these factors to maximize effectiveness. A well-thought-out layout not only improves safety but also enhances the overall flow of traffic.
Compliance with Local and Federal Safety Guidelines
Adhering to safety guidelines is non-negotiable when setting up traffic cones. The MUTCD and OSHA provide clear standards for cone size, color, and placement. Following these rules ensures your traffic management plan meets legal requirements and protects everyone involved.
For example, the MUTCD specifies that cones used on highways must be at least 28 inches tall and include reflective materials. OSHA emphasizes the importance of using cones that can withstand impact without causing damage. By complying with these guidelines, you create a safer environment for both workers and drivers.
Regular inspections also help maintain compliance. Check cones for wear and tear, and replace damaged ones immediately. Staying proactive ensures your setup remains effective and meets all safety standards.
Regular Maintenance and Inspection of Traffic Cones
Regular maintenance and inspection of traffic cones are essential to ensure their effectiveness in any work zone or traffic management plan. You can’t afford to overlook this step, as damaged or worn-out cones compromise safety and disrupt the flow of traffic. By keeping your cones in top condition, you maintain a professional and secure environment for both workers and drivers.
Start by inspecting your cones for visible damage. Look for cracks, fading colors, or missing reflective bands. These issues reduce the cone’s visibility and effectiveness, especially in low-light conditions or high-speed areas. Replace cones that show significant wear and tear. A cone that can’t stand upright or has lost its bright orange color no longer serves its purpose.
Cleaning your cones regularly also makes a big difference. Dirt and grime can dull their appearance, making them harder to spot. Use a mild detergent and water to clean them, ensuring they remain vibrant and noticeable. For cones used in areas with heavy traffic or construction dust, more frequent cleaning may be necessary.
Storage plays a crucial role in extending the lifespan of your cones. Keep them in a dry, shaded area to prevent damage from prolonged exposure to sunlight or harsh weather. UV rays can cause the material to weaken and the color to fade. Stack cones properly to avoid deformation, which can affect their stability when deployed.
Routine checks should be part of your traffic management plan. Schedule inspections before and after each use. This habit helps you identify issues early and ensures your cones are always ready for deployment. By prioritizing maintenance, you not only save money on replacements but also enhance the overall safety of your work zones.
“Well-maintained traffic cones are the backbone of an effective traffic control system.” – Federal Highway Administration
Taking these steps ensures your cones remain reliable tools in your traffic management efforts. A little care goes a long way in keeping your work zones safe and efficient.
Traffic cones are more than just bright markers; they are essential tools in creating a safe and organized environment. By understanding their role in your traffic management plan, you can ensure smoother traffic flow and better protection for everyone involved. Proper placement and the right quantity of cones make a significant difference in safety and efficiency. When you follow best practices and plan thoughtfully, you not only meet regulations but also create a safer space for workers, drivers, and pedestrians alike.
FAQ
How many traffic cones are needed for a 100-meter work zone?
The number of cones depends on factors like road width, traffic speed, and the type of work being done. For urban construction zones, you might need dozens of cones to guide traffic effectively. Longer taper lengths on high-speed roads require more cones, while low-speed areas may need fewer. Using data to analyze traffic flow and road conditions helps you determine the exact number.
Why is proper cone placement so important?
Proper placement ensures safety and smooth traffic flow. Misplaced cones can confuse drivers, leading to accidents. For example, a tragic highway accident occurred when cones were improperly placed, causing a car to veer into another lane. This incident resulted in the death of a child and injuries to others. Following placement guidelines, like using taper formations, prevents such tragedies and keeps everyone safe.
How do you estimate the number of cones for parking lots?
To estimate cone requirements, consider the size of the parking lot and the number of entrances and spaces. For example, a supermarket parking lot with 200 spaces may need around 50 traffic cones to manage entry points, pedestrian pathways, and restricted areas. Larger lots or those hosting events may require additional cones for smooth traffic management.
How do traffic cones contribute to emergency response?
Traffic cones play a critical role in managing accident sites and emergencies. They create safe perimeters, guide traffic, and protect responders. Emergency vehicles should carry at least 16 cones, as recommended by the MUTCD, to redirect traffic effectively. Proper cone placement minimizes confusion and ensures safety during high-pressure situations.
Are there global differences in traffic cone usage?
Yes, traffic cone usage varies worldwide. Some countries, like the United States, use millions of cones annually due to extensive roadwork and infrastructure projects. Fun fact: large-scale construction projects in the U.S. can use hundreds of thousands of cones. Globally, the total number of traffic cones exceeds 50 million, reflecting their importance in traffic management.
How can you balance cost and safety when using traffic cones?
Balancing cost and safety involves analyzing factors like road conditions, traffic volume, and project scale. Using too few cones compromises safety, while overusing them increases costs. For example, a 100-meter stretch of road work may need dozens of cones, depending on the complexity. Data-driven decisions help you find the right balance, ensuring safety without overspending.