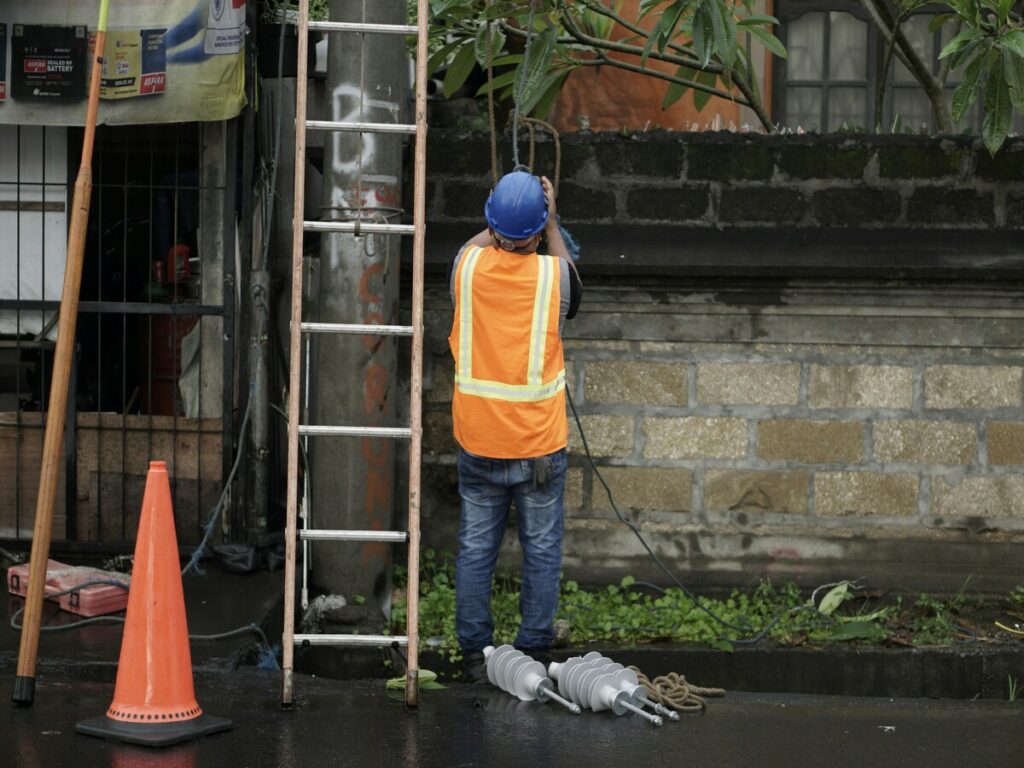
Zones de travail et les sites d'emploi peuvent présenter des risques graves sans mesures de sécurité appropriées. Règlement sur le cône de la circulation OSHA vous aider à créer un environnement plus sûr en fixant des normes claires. Ces règles s'assurent que les cônes sont visibles, durable, et correctement placé pour protéger les travailleurs et le public. Suivre ces réglementations de sécurité minimise les accidents et maintient votre site conforme à votre site. En comprenant et en appliquant ces directives, Vous faites une étape essentielle vers le maintien de la sécurité au travail.
Pour vous assurer que votre lieu de travail répond aux normes de sécurité de l'OSHA, vous pouvez explorer l'optraffique Cônes de circulation conformes à l'OSHA Et choisissez les produits qui conviennent le mieux à vos besoins. Contactez-nous aujourd'hui Pour obtenir des conseils d'experts et trouver la solution de cône de trafic parfaite pour votre site - construit pour la sécurité, durabilité, et pleine conformité.
Comprendre les réglementations du cône de trafic OSHA
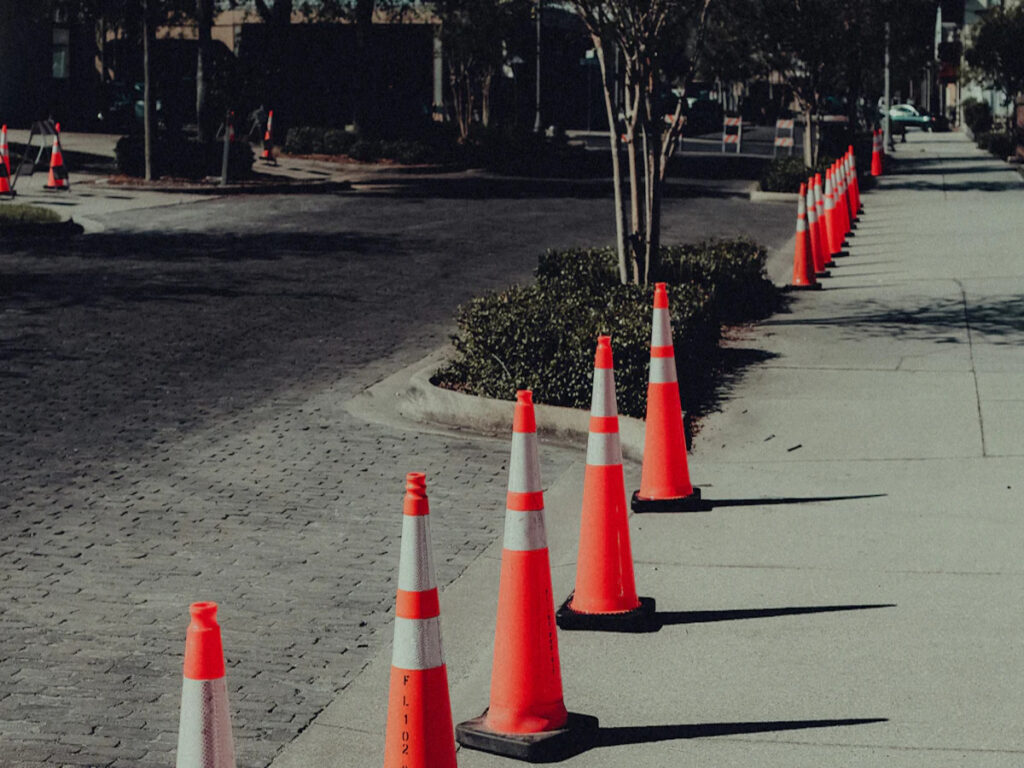
Normes de taille et de hauteur
Exigences de hauteur minimale pour différentes zones de travail
Hauteur du cône de trafic joue un rôle essentiel pour assurer la visibilité et la sécurité dans les zones de travail. Règlement sur le cône de la circulation OSHA Spécifiez les exigences de hauteur minimale suivantes:
- Les cônes utilisés sur les autoroutes doivent être au moins 28 pouces grand.
- Des cônes plus hauts sont recommandés pour les routes à grande vitesse afin de s'assurer qu'elles sont facilement visibles pour les conducteurs.
Ces normes de cônes de trafic vous aident à sélectionner les bons cônes de travail pour votre zone de travail, Assurer la conformité et réduire les risques.
Pour une sécurité améliorée, Envisagez d'opter pour de haute qualité, des options durables telles que Cônes de trafic Optraffic à vendre, qui répondent ou dépassent les normes de hauteur de l'OSHA pour une visibilité et une fiabilité maximales dans divers environnements.
Considérations spéciales pour les cônes d'utilisation nocturne
Les zones de travail nocturnes ont besoin de cônes de travail avec une visibilité améliorée. Les matériaux réfléchissants sont essentiels pour les cônes utilisés dans des conditions de faible luminosité. Ces matériaux permettent aux phares d'éclairer les cônes de travail, les rendre visibles à distance. Vous devriez également envisager d'utiliser des cônes de travail plus grands la nuit pour améliorer davantage la visibilité.
Conseil: Vérifiez toujours que vos cônes de trafic rencontrent le Manuel sur les dispositifs de contrôle de la circulation uniformes (Mutcd) Lignes directrices pour une utilisation nocturne.
Conditions de visibilité
Matériaux réfléchissants pour les conditions de faible luminosité
OSHA Mandate l'utilisation de bandes réfléchissantes sur les cônes de travail pour les conditions de faible luminosité ou nocturnes. Ces bandes améliorent la visibilité et garantissent la conformité aux lois sur les cônes de la circulation. Le Mutcd nécessite également des matériaux réfléchissants pour les cônes de travail utilisés sur les routes à grande vitesse.
Fonctionnalité | Description |
---|---|
Couleur | Orange vif, Un signal universel pour la prudence, Assurer une visibilité immédiate. |
Bandes réfléchissantes | Requis pour les cônes utilisés sur les routes à grande vitesse ou la nuit pour améliorer la visibilité dans des conditions de faible luminosité. |
Référence de la conformité | MUTCD oblige des matériaux réfléchissants pour les cônes de trafic dans des scénarios à faible luminosité. |
Couleurs approuvées par l'OSHA pour une visibilité maximale
L'orange vif est la couleur standard pour les cônes de trafic, car il signale la prudence et attire l'attention. Cette couleur garantit que les cônes se démarquent dans divers environnements, Des zones de construction aux espaces publics. En utilisant Couleurs approuvées par l'OSHA Vous aide à vous conformer aux réglementations de sécurité et améliore l'efficacité de vos dispositifs de contrôle de la circulation.
Durabilité et normes matérielles
Matériaux résistants aux intempéries à usage extérieur
Les cônes de circulation doivent résister aux conditions météorologiques difficiles pour rester efficace. L'OSHA recommande d'utiliser des cônes fabriqués à partir de matériaux durables comme le plastique renforcé, PVC, ou caoutchouc. Ces matériaux résistent à la fissuration, décoloration, et brisant, Même à des températures extrêmes.
Matériel | Description |
---|---|
PVC | Flexible et résilient, Idéal pour une utilisation en plein air, résiste à la fissuration et à la décoloration à des températures extrêmes. |
Caoutchouc | Offre une excellente stabilité et une résistance à l'impact, Convient aux zones à fort trafic. |
Cônes lourds pour les zones à fort trafic
Les zones à trafic élevé exigent des cônes qui peuvent supporter des impacts fréquents et une utilisation intensive. Les cônes en caoutchouc offrent une excellente stabilité et une résistance à l'impact, les rendre idéaux pour ces situations. En choisissant des cônes robustes, Vous vous assurez de la conformité avec Normes de sécurité de la barricade OSHA et maintenir un environnement de travail sûr.
Note: Les cônes de circulation durables réduisent les coûts de remplacement et assurent la conformité à long terme avec les réglementations du cône de la circulation OSHA.
Placement et utilisation du cône de trafic selon les réglementations du cône de la circulation OSHA
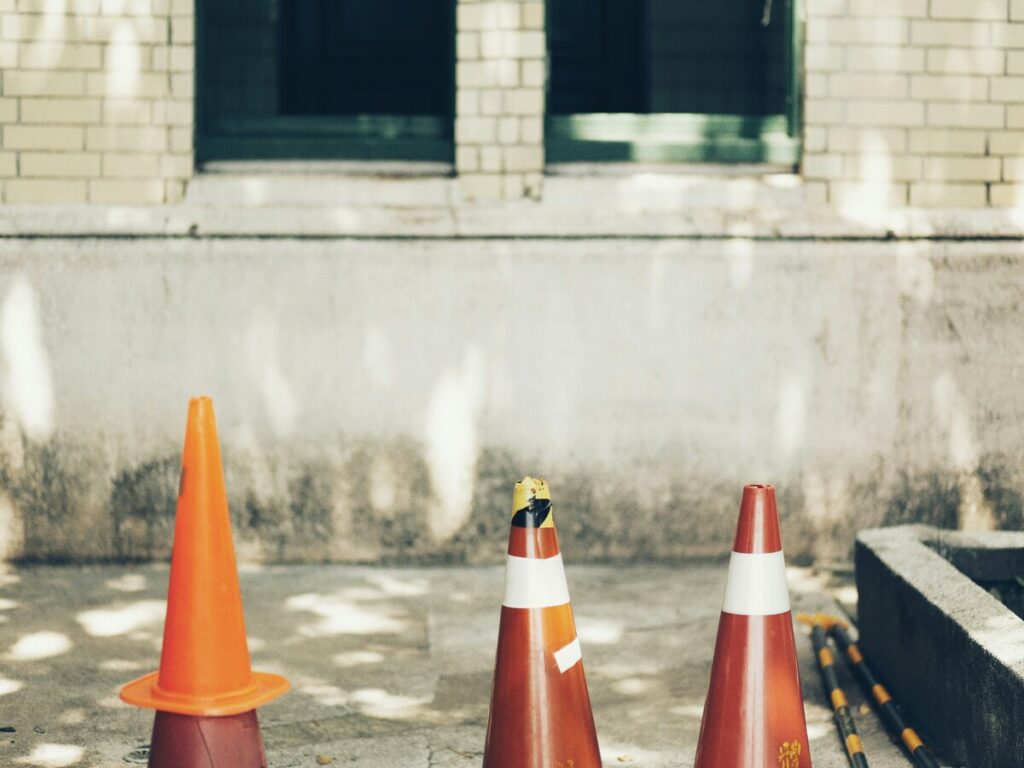
Directives de placement des cônes de trafic
Espacement approprié entre les cônes dans les zones de travail
L'espacement approprié des cônes de circulation garantit des conseils clairs pour les conducteurs et améliore la sécurité dans les zones de travail. Le Manuel sur les dispositifs de contrôle de la circulation uniformes (Mutcd) recommande un 20:1 débit. Cela signifie pour chaque 20 pieds de fermeture de voie, Le cône doit s'étendre d'un pied. Sur les autoroutes, Les cônes routiers doivent être espacés plus loin pour donner aux conducteurs suffisamment de temps pour réagir. Pour les routes à basse vitesse, Un espacement plus proche fournit de meilleurs conseils. L'ajustement de l'espacement en fonction du type de route et de la limite de vitesse garantit la conformité aux réglementations du cône de circulation OSHA et améliore le flux de trafic.
Placement basé sur la vitesse du véhicule et le flux de trafic
La vitesse du véhicule a un impact significatif sur la façon dont vous placez les cônes de circulation. Pour les zones à grande vitesse, Des cônes plus hauts avec des colliers réfléchissants améliorent la visibilité. L'espacement adéquat entre les cônes permet aux conducteurs plus de temps pour réagir et ralentir. Dans les zones à basse vitesse, Les cônes peuvent être placés plus près pour créer un chemin clair. Envisagez toujours le flux de trafic et réglez le placement du cône pour maintenir l'ordre et la sécurité dans la zone de travail.
Applications situationnelles
Placement du cône de trafic de chantier
Dans les chantiers de construction, Le placement correct du cône de trafic est crucial pour la sécurité des travailleurs et des conducteurs. Faire face à la circulation lors de la mise en place de cônes pour assurer la visibilité. Maintenir un espacement minimum de 30 pieds entre les cônes de construction et positionnez-les au moins 200 pieds de la zone de travail pour fournir un avertissement ample. Utilisez des cônes de route supplémentaires pour marquer les dangers ou les obstacles. Pour les zones à grande vitesse, Les cônes de construction doivent être au moins 28 pouces de haut, tandis que les cônes de 18 pouces fonctionnent bien dans les zones à basse vitesse.
Lignes directrices sur les travaux routiers et l'espace public
Pour les travaux routiers et les espaces publics, Les cônes de route doivent guider la circulation loin de la zone de travail en utilisant un modèle de rétrécissement. Positionner les cônes de route autour 250 pieds du début de la zone de travail pour donner aux conducteurs suffisamment de temps pour s'adapter. Conseils de route spatiaux uniformément pour créer une barrière cohérente. Utilisez des colliers réfléchissants pour une visibilité nocturne et assurez-vous que les cônes répondent aux normes OSHA pour les appareils de contrôle de la circulation.
Améliorer la visibilité
Éviter les obstructions qui bloquent les cônes
Les obstructions peuvent réduire l'efficacité des cônes de circulation. Vérifiez toujours les objets comme les véhicules garés, équipement, ou débris qui pourraient bloquer les cônes de la vue. Effacer ces obstructions pour maintenir la visibilité et assurer la conformité aux lois sur les cônes de la circulation.
En utilisant un éclairage ou une signalisation supplémentaire si nécessaire
Dans des conditions de faible luminosité, L'éclairage ou la signalisation supplémentaire améliore la visibilité du cône. Utiliser lumières portables ou signes illuminés pour attirer l'attention sur la zone de travail. Ces appareils de canalisation améliorent la sécurité et aident les conducteurs à naviguer en toute sécurité dans la zone. Combinant des cônes avec d'autres outils de barricade Assure le respect des réglementations de l'OSHA et réduit les risques.
Entretien et inspection pour la conformité avec les réglementations du cône de trafic OSHA
Pratiques d'inspection régulières
Identifier l'usure
L'inspection de vos cônes de trafic vous aide régulièrement à identifier les signes d'usure. Chercher des fissures, bosses, ou décolorer les couleurs qui pourraient réduire leur visibilité et leur efficacité. Les cônes endommagés peuvent ne pas répondre aux normes de sécurité de la barricade OSHA, mettre en danger les travailleurs et les conducteurs. Les inspections fréquentes garantissent que vos cônes de trafic restent conformes aux lois sur les cônes de trafic et maintiennent leur rôle en tant que dispositifs de contrôle du trafic efficaces.
Assurer la réflectivité reste intacte
Matériaux réfléchissants sur les cônes réfléchissants jouent un rôle vital dans les conditions de faible luminosité. Au fil du temps, saleté, Débris, et l'exposition aux intempéries peut diminuer leur réflectivité. Vérifiez les bandes de réflexion lors des inspections pour vous assurer qu'ils restent intacts et fonctionnels. Si les bandes semblent ternes ou endommagées, Remplacez-les immédiatement pour se conformer aux réglementations du cône de circulation de l'OSHA et maintenir la sécurité dans votre zone de travail.
Conseils de nettoyage et de stockage
Méthodes de nettoyage pour maintenir la visibilité du cône
Garder vos cônes de travail est essentiel pour préserver leur visibilité et leur conformité avec les réglementations de l'OSHA. Utilisez ces méthodes pour maintenir leur efficacité:
- Laver les cônes de travail avec du savon et de l'eau modérés pour éliminer la saleté, Débris, et polluants.
- Rincer soigneusement pour éviter l'accumulation de résidus.
- Laisser les cônes de travail sécher complètement avant de les stocker.
Le nettoyage régulier garantit que les couleurs vives et les matériaux réfléchissants restent efficaces, surtout dans les zones à fort trafic.
Stockage approprié pour éviter les dommages
Le stockage approprié prolonge la durée de vie de vos cônes de travail et les maintient conformes aux normes de sécurité de la barricade OSHA. Suivez ces meilleures pratiques:
- Stocker les cônes de circulation debout dans un nettoyage, zone sèche pour éviter la déformation.
- Évitez la lumière directe du soleil et des températures extrêmes pour protéger le matériau.
- Empiler les cônes soigneusement pour économiser de l'espace et maintenir leur forme.
- Inspectez périodiquement des cônes de circulation stockés pour les fissures ou la décoloration.
Ces étapes vous aident à maintenir l'intégrité structurelle de vos cônes de trafic et à vous assurer qu'ils restent fiables à canaliser les appareils.
Remplacement des cônes non conformes
Signes Un cône a besoin de remplacement
Reconnaître quand un cône de travail a besoin de remplacement est crucial pour maintenir la conformité. Remplacer les cônes si vous remarquez:
- Fissure, bosses, ou d'autres dommages structurels.
- Couleurs fanées qui réduisent la visibilité.
- Les bandes réfléchissantes qui ne fonctionnent plus efficacement.
L'utilisation de cônes de travail endommagés peut entraîner la non-conformité des réglementations du cône de trafic OSHA et des compromis sur la sécurité dans votre zone de travail.
Meilleures pratiques pour le remplacement en temps opportun
Le remplacement en temps opportun des cônes non conformes garantit que votre zone de travail reste sûre et répond aux normes de l'OSHA. Gardez un stock de cônes de rechange pour remplacer les endommagés immédiatement. Effectuer des inspections régulières pour identifier les cônes qui doivent être remplacés avant de présenter un risque. En restant proactif, Vous maintenez la conformité et protégez les travailleurs et le public.
Éviter les erreurs courantes
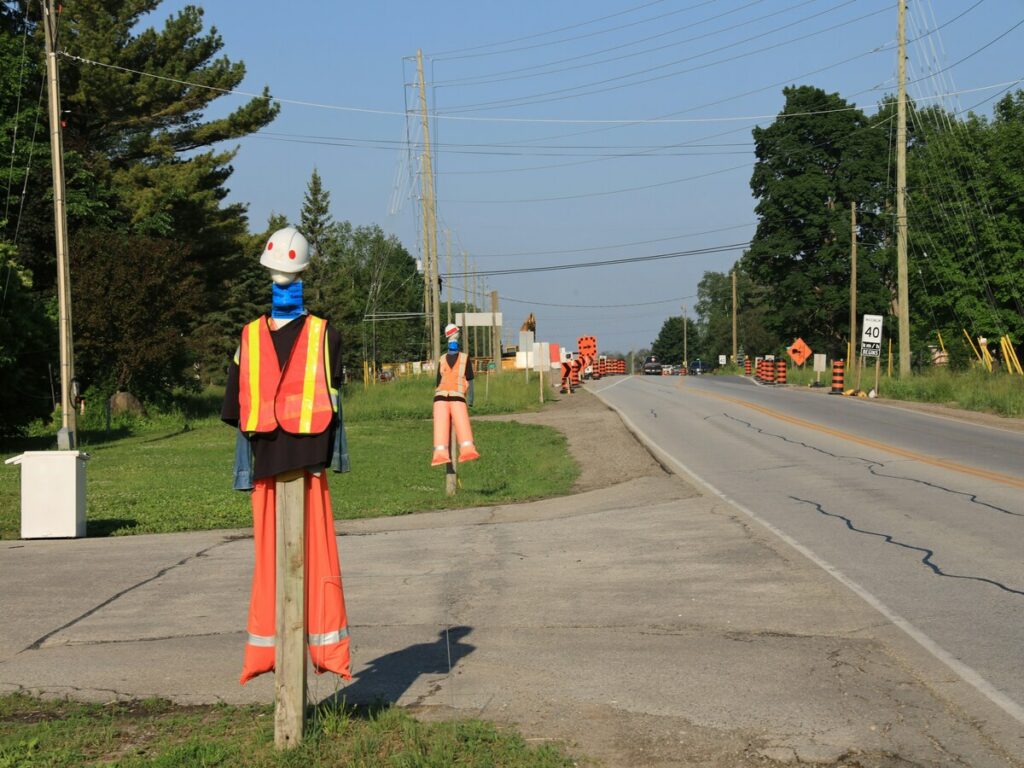
En utilisant des cônes non conformes
Risques de non-conformité aux normes de l'OSHA
L'utilisation de cônes non conformes dans les zones de contrôle de la circulation peut entraîner de graves conséquences. Vous risquez de violer les réglementations de l'OSHA, qui peut entraîner des inspections et des citations. Le non-respect du MUTCD peut également créer des conditions dangereuses pour les travailleurs et les piétons. Cela augmente la probabilité d'accidents et de responsabilité pour votre organisation. En plus, Les cônes de sécurité qui ne respectent pas les normes de sécurité peuvent ne pas fournir un avertissement adéquat, laisser des piétons et des conducteurs vulnérables aux dangers.
Conseil: Assurez-vous toujours que vos cônes de trafic répondent aux exigences de l'espacement et de la longueur du conique du MUTCD pour maintenir une canalisation appropriée du trafic.
Comment vérifier la conformité avant d'acheter
Avant d'acheter des cônes de trafic, Vérifiez leur conformité avec les normes OSHA et MUTCD. Recherchez des cônes fabriqués à partir de matériaux durables comme du PVC ou du caoutchouc, Comme ceux-ci sont conçus pour une utilisation à long terme. Vérifiez les bandes réfléchissantes et assurez-vous que les cônes de trafic sont orange vif pour une visibilité maximale. Passez en revue les spécifications du fabricant Pour confirmer que les cônes de trafic répondent aux exigences de hauteur et de durabilité. En prenant ces mesures, Vous pouvez éviter d'investir dans des cônes de circulation qui ne respectent pas les normes de sécurité.
Placement de cône de trafic incorrect
Placer des cônes trop proches ou trop éloignés
Le placement incorrect de cône de circulation peut confondre les conducteurs et réduire la sécurité. Placer les cônes trop proches les uns des autres crée un surpopulation, Tout en les espaçant trop éloignés diminue leur efficacité. Pour éviter ces erreurs, maintenir une distance cohérente d'environ 20 pieds entre les cônes dans les zones de contrôle de la circulation temporaires. Pour les chantiers de construction, commencer à placer des cônes approximativement 40 pas de la zone de travail. Cela garantit la clarté et les conseils appropriés pour les conducteurs.
Ignorer la vitesse du trafic et les considérations de flux
La vitesse de la circulation et le débit jouent un rôle essentiel dans le placement du cône. Dans les zones à grande vitesse, Utilisez des cônes plus hauts et augmentez l'espacement pour donner aux conducteurs plus de temps pour réagir. Pour les zones à basse vitesse, Un espacement plus proche crée un chemin clair. Évaluez toujours l'environnement du point de vue d'un conducteur pour vous assurer que les cônes de l'allée sont facilement vus par les piétons et les automobilistes. Le placement approprié améliore la sécurité et garantit le respect des directives de placement des cônes de trafic OSHA.
Négligence
Permettre aux cônes de se décolorer ou d'endommager
Négliger la maintenance peut conduire à délavé ou cônes endommagés, réduire leur visibilité et leur efficacité. Cela augmente le risque d'accidents, surtout la nuit. Le nettoyage et les inspections régulières sont essentiels pour garder les cônes en bon état. Laver les cônes avec du savon et de l'eau pour enlever la saleté, et vérifier les fissures ou les bandes de réflexion usées. Les cônes endommagés doivent être remplacés immédiatement pour maintenir la conformité et la sécurité.
Surplombant les inspections et les remplacements réguliers
Sauter des inspections régulières peut entraîner des cônes non conformes à utiliser. Inspectez fréquemment vos cônes pour identifier l'usure. Remplacez les cônes par des dommages structurels ou des couleurs fanées pour s'assurer qu'elles restent efficaces à canaliser les appareils. Garder un stock de cônes de rechange vous permet de remplacer rapidement ceux endommagés, Assurer que votre zone de travail reste en sécurité et conforme.
Adhérer aux réglementations du cône de la circulation de l'OSHA assure un lieu de travail plus sûr et réduit les risques pour les travailleurs et le public. Le placement approprié des cônes dans chaque zone minimise les dangers et dirige efficacement le trafic. Entretien régulier, y compris le nettoyage et les inspections, garde les cônes visibles et conformes. Investir dans des dispositifs de canalisation durables comme le PVC ou les cônes en caoutchouc réduit les coûts à long terme et améliore la sécurité.
Les cônes de circulation agissent comme des barricades essentielles, guider les véhicules et les piétons tout en empêchant les accidents. En suivant les normes de l'OSHA, Vous créez un environnement sécurisé et maintenez des opérations en douceur. La conformité cohérente protège tout le monde et garantit que votre chantier répond aux exigences de sécurité.