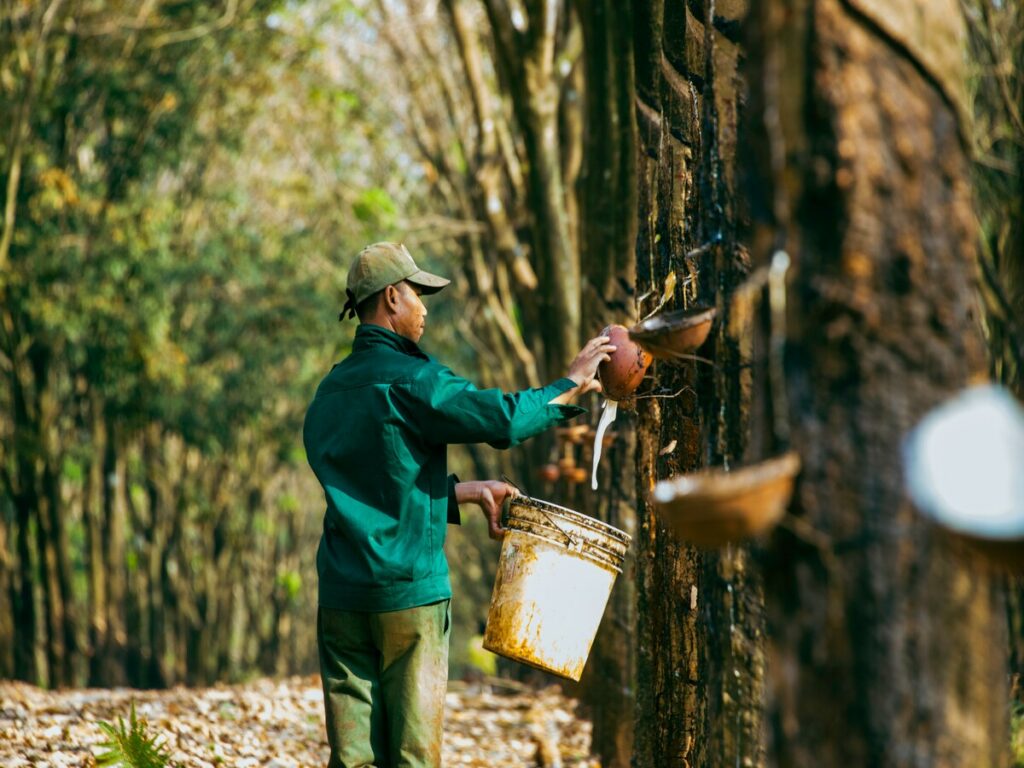
Cônes de sécurité en caoutchouc représenter un mélange remarquable de la nature et de l'innovation. Ces outils essentiels reposent sur deux sources primaires: caoutchouc naturel, dérivé de la sève des caoutchoucs, et caoutchouc synthétique, créé par des processus industriels avancés. Caoutchouc naturel, souvent appelé le “Arbre de la vie,” a été une ressource vitale depuis des siècles. Caoutchouc synthétique, développé pendant la révolution industrielle, élargi ses applications. Ensemble, Ces matériaux forment le fondement du cône de sécurité, Assurer la durabilité et la flexibilité. Cette combinaison met en évidence comment le caoutchouc continue de façonner les solutions de sécurité modernes.
L'histoire et les origines du caoutchouc
Le caoutchouc a une histoire fascinante qui s'étend sur des siècles, Mélanger la découverte naturelle avec l'innovation industrielle. Son voyage de la matière première à usage quotidien reflète l'ingéniosité du progrès humain.
Caoutchouc naturel: L'arbre de vie
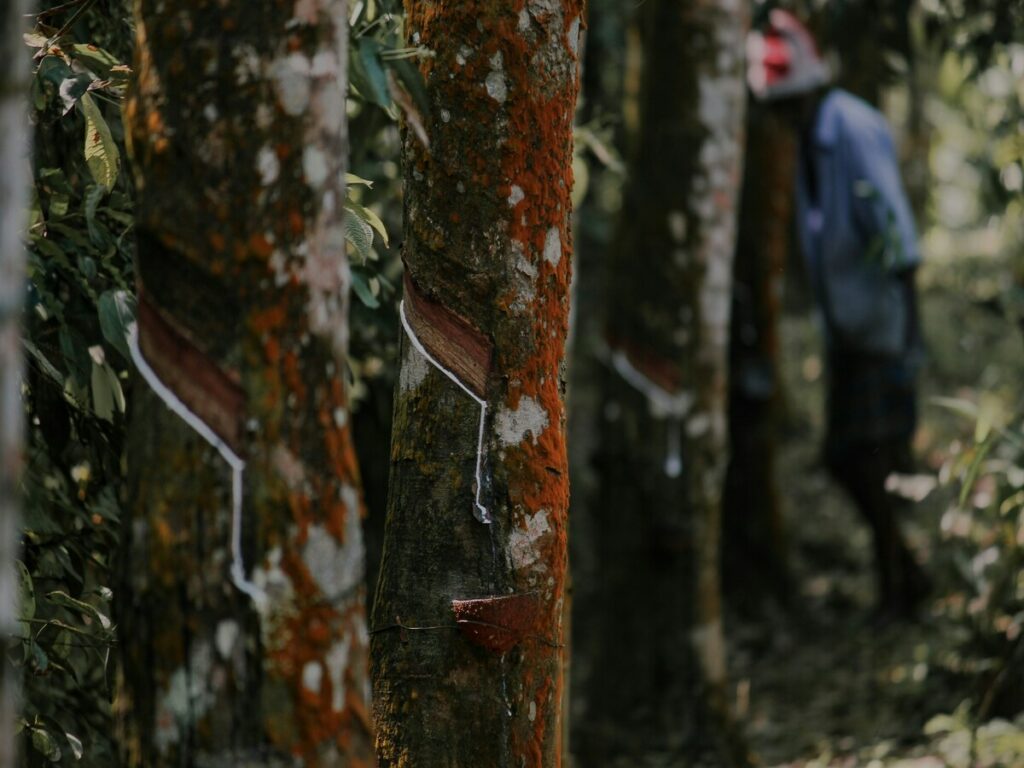
Le caoutchouc naturel provient de la sève du Hevea Brassilensis arbre, communément appelé le caoutchouc. Les peuples autochtones en Amérique du Sud ont d'abord découvert ses propriétés uniques. Ils ont utilisé la sève de l'arbre pour créer des articles imperméables, Reconnaître son élasticité et sa résilience. Lorsque les explorateurs européens ont rencontré ce matériel, Ils l'ont présenté au reste du monde, susciter un intérêt généralisé.
Le 19e siècle a marqué un tournant pour le caoutchouc naturel. Dans 1839, Charles Goodyear a révolutionné sa convivialité en découvrant vulcanisation. Ce processus impliquait un chauffage en caoutchouc avec du soufre, le rendre plus fort et plus durable. La vulcanisation a transformé le caoutchouc en un matériau polyvalent, alimenter le boom industriel et étendre ses applications dans des produits comme les pneus, tuyaux, et équipements de sécurité.
«Le caoutchouc est l'arbre de la vie,"Une phrase souvent utilisée pour décrire son importance, Souligne comment cette ressource naturelle a soutenu les industries et les communautés du monde entier.
Caoutchouc synthétique: Une révolution industrielle
La demande de caoutchouc a augmenté au début du 20e siècle, surtout pendant la Seconde Guerre mondiale. Cependant, L'accès au caoutchouc naturel s'est limité en raison des conflits géopolitiques. Pour relever ce défi, les chimistes ont travaillé sans relâche pour créer une alternative. Leurs efforts ont conduit à l'invention du caoutchouc synthétique, un matériau fabriqué à partir de composés à base de pétrole.
Dans 1940, Les États-Unis ont établi le Société de réserve de caoutchouc (RRC) Pour fixer une alimentation stable en caoutchouc synthétique. Cette initiative a assuré que les industries pouvaient continuer à produire des produits essentiels, Même quand le caoutchouc naturel était rare. Le caoutchouc synthétique offrait plusieurs avantages, y compris la résistance aux températures et aux produits chimiques extrêmes, Le rendre idéal pour les applications industrielles et militaires.
Aujourd'hui, Le caoutchouc synthétique complète le caoutchouc naturel dans d'innombrables produits, y compris les cônes de sécurité que vous voyez sur les routes et les chantiers de construction.
La chaîne d'approvisionnement en caoutchouc mondiale
La production de caoutchouc repose sur une chaîne d'approvisionnement mondiale complexe. Le caoutchouc naturel provient principalement de régions tropicales comme l'Asie du Sud-Est, où des pays comme la Thaïlande, Indonésie, et la Malaisie domine la production. Les agriculteurs récoltent le latex des arbres en caoutchouc, qui est ensuite traité et exporté vers les fabricants du monde entier.
Caoutchouc synthétique, d'autre part, dépend des industries pétrochimiques. Pays ayant des capacités de fabrication chimique avancées, comme les États-Unis, Allemagne, et la Chine, jouer un rôle important dans sa production. Ces nations affinent l'huile brute dans les matières premières nécessaires pour produire du caoutchouc synthétique.
La chaîne d'approvisionnement en caoutchouc mondiale relie les agriculteurs, chimiste, et fabricants, S'assurer que ce matériel essentiel atteint les industries du monde entier. Qu'il soit naturel ou synthétique, Le caoutchouc continue de façonner la vie moderne, des pneus de votre voiture aux cônes de sécurité qui vous guident sur la route.
Du caoutchouc brut au matériau utilisable
Traitement du caoutchouc naturel
Le caoutchouc naturel commence son voyage en latex, un liquide laiteux récolté par Hevea Brassilensis arbre. Les agriculteurs collectent ce latex en faisant de petites incisions dans l'écorce, Permettre à la sève de s'écouler dans des conteneurs. Une fois rassemblé, Le latex subit plusieurs étapes pour la transformer en matériau utilisable.
D'abord, Le latex est filtré pour éliminer les impuretés. Alors, il est mélangé avec des acides pour coaguler, ou solidifier, les particules de caoutchouc. Ce caoutchouc coagulé est pressé dans des draps et séché, Utilisation souvent de la fumée ou de la chaleur. Ces feuilles, Connu sous le nom de caoutchouc brut, sont ensuite expédiés aux fabricants du monde entier. Le processus garantit que le caoutchouc conserve son élasticité et sa force, Le rendre adapté à diverses applications, y compris les cônes de sécurité.
Fabrication de caoutchouc synthétique
Le caoutchouc synthétique suit un chemin différent. Les chimistes le créent en laboratoires utilisant des composés à base de pétrole. Le processus commence par raffiner du pétrole brut pour extraire des monomères comme butadiène et styrène. Ces monomères subissent une polymérisation, une réaction chimique qui les relie à de longues chaînes, formant du caoutchouc synthétique.
Contrairement au caoutchouc naturel, Le caoutchouc synthétique peut être adapté pour répondre aux besoins spécifiques. Par exemple, Les fabricants peuvent ajuster sa résistance à la chaleur, produits chimiques, ou porter. Cette personnalisation rend le caoutchouc synthétique idéal pour les utilisations industrielles, comme les cônes de circulation, où la durabilité et la flexibilité sont cruciales. La capacité de produire du caoutchouc synthétique à la demande assure également une offre régulière, Quelle que soit la disponibilité du caoutchouc naturel.
Vulcanisation: Renforcement du caoutchouc pour la durabilité
Qu'il soit naturel ou synthétique, Le caoutchouc brut nécessite une vulcanisation pour obtenir son plein potentiel. La vulcanisation implique le chauffage du caoutchouc avec du soufre ou d'autres agents de durcissement. Ce processus crée de fortes liaisons chimiques entre les molécules du caoutchouc, formant un matrice tridimensionnelle. Le résultat est un matériau non seulement plus fort mais aussi plus élastique et résistant à l'usure.
Pour les cônes de sécurité, La vulcanisation garantit qu'ils peuvent supporter des conditions dures, impacts, et utilisation constante. La résistance et la flexibilité améliorées fournies par la vulcanisation font du caoutchouc le choix idéal pour ces outils essentiels.
Signes OPT Les cônes de sécurité en caoutchouc sont conçus pour la durabilité et la fiabilité, En leur faisant le choix parfait pour une large gamme d'applications de contrôle du trafic.
Pourquoi le caoutchouc est le matériau idéal pour les cônes de circulation
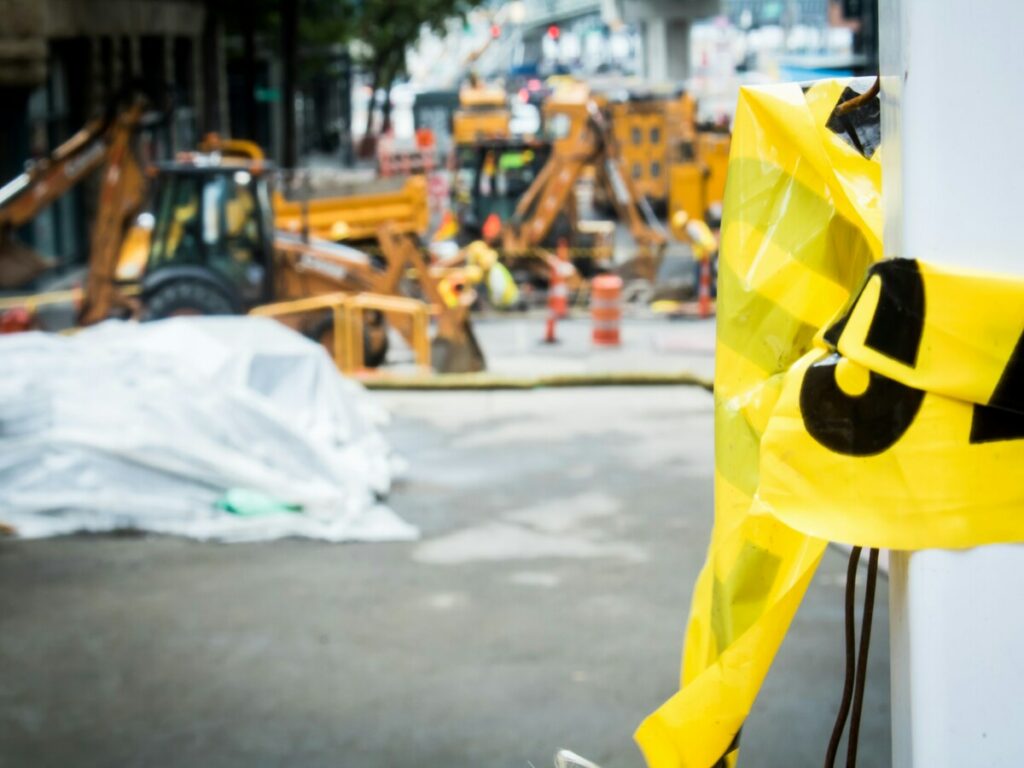
Cônes de signalisation jouer un rôle crucial pour assurer la sécurité et l'ordre dans divers environnements. Le caoutchouc se distingue comme le matériau idéal pour ces cônes de circulation en raison de ses propriétés uniques et de sa capacité à répondre aux normes de sécurité élevées. Explorons pourquoi les cônes de trafic en caoutchouc excellent dans les performances et la fiabilité.
Propriétés clés du caoutchouc
Le caoutchouc offre une combinaison de résistance, flexibilité, et la durabilité qui le rend parfait pour les cônes de circulation. Contrairement aux autres matériaux, Les cônes en caoutchouc sont plus lourds, ce qui les aide à rester droits même dans des conditions difficiles. Les vents violents ou les bosses accidentelles ne les feront pas facilement bas, s'assurer qu'ils restent en place pour guider efficacement le trafic.
Les cônes de trafic en caoutchouc présentent également une excellente résistance aux temps. Ils peuvent supporter des températures extrêmes sans se fissurer ou se déformer. Qu'il soit exposé à une chaleur torride ou à un froid glacial, Le caoutchouc maintient son intégrité structurelle. Cette durabilité garantit que les cônes durent plus longtemps, Réduire le besoin de remplacements fréquents.
Une autre propriété clé du caoutchouc est sa résistance aux UV. Une exposition prolongée à la lumière du soleil ne fait pas disparaître les couleurs. Cette fonctionnalité garantit que les cônes conservent leur brillant, Haute visibilité même après une utilisation extérieure prolongée. Les couleurs vibrantes aident les conducteurs et les piétons à remarquer les cônes à distance, Améliorer la sécurité dans les zones animées.
Caractéristiques de sécurité et de visibilité
Les cônes de trafic en caoutchouc sont conçus avec la sécurité et la visibilité comme priorités supérieures. Leur poids et leur stabilité les empêchent d'être facilement déplacés, qui est essentiel pour maintenir des limites claires dans les zones de construction ou sur les routes. Cette stabilité garantit que les cônes répondent constamment aux normes de sécurité, Fournir des conseils fiables dans les zones à haut risque.
La haute visibilité des cônes de sécurité en caoutchouc est une autre caractéristique hors concours. Leurs couleurs vives, Souvent amélioré avec des bandes réfléchissantes, les rendre perceptibles de jour et de nuit. Cette visibilité réduit le risque d'accidents en alertant les conducteurs et les piétons aux dangers potentiels. Que ce soit dans des conditions de faible luminosité ou sous la lumière directe du soleil, Ces cônes restent faciles à repérer.
La flexibilité du caoutchouc contribue également à la sécurité. Lorsque les véhicules ont accidentellement frappé un cône, Le matériau absorbe l'impact sans se casser. Cela réduit la probabilité de dommages aux véhicules ou aux blessures aux individus. La combinaison de la durabilité, visibilité, et la résistance à l'impact garantit que les cônes de trafic en caoutchouc fonctionnent efficacement dans divers environnements.
Le processus de fabrication des cônes de sécurité en caoutchouc
La création de cônes de sécurité en caoutchouc implique un processus méticuleux qui assure leur durabilité, flexibilité, et la fiabilité. Chaque étape du processus de fabrication contribue à la capacité du cône à résister aux conditions difficiles et à maintenir sa fonctionnalité au fil du temps.
Concevoir et façonner le moule
Le voyage commence par la conception du moule. Les fabricants arborent des moules pour définir la forme du cône, taille, et caractéristiques structurelles. Ces moules sont généralement fabriqués à partir de matériaux à haute résistance pour supporter une utilisation répétée pendant la production. Le processus de conception se concentre sur la réalisation d'une structure en une seule pièce, ce qui améliore la stabilité du cône et réduit les points faibles.
Une fois le moule prêt, matières premières, comme le caoutchouc naturel ou synthétique, sont préparés à la mise en forme. Le caoutchouc est chauffé à un état souple et versé ou pressé dans le moule. Cette étape garantit que le cône prend sa forme effilée emblématique avec une large base pour la stabilité. Le centre de gravité bas, réalisé grâce à cette conception, empêche le cône de basculer facilement, Même dans des environnements venteux ou à fort trafic.
Durcissement et renforcement du caoutchouc
Après la mise en forme, Le caoutchouc subit un durcissement pour améliorer sa résistance et sa flexibilité. Ce processus, souvent appelé vulcanisation, implique d'exposer le caoutchouc moulé à des températures élevées et une pression. La vulcanisation crée de fortes liaisons chimiques dans le caoutchouc, le rendre plus durable et résistant à l'usure.
La vulcanisation à la vapeur à haute température est une méthode courante utilisée dans la fabrication de cônes de sécurité en caoutchouc. Cette technique garantit que les cônes peuvent supporter des températures extrêmes, allant de -30 ° F à 150 ° F, sans se craquer ou déformer. Le caoutchouc durci gagne également la capacité de résister aux impacts lourds, Permettre au cône de revenir à sa forme d'origine même après avoir été tordu ou comprimé.
«Les cônes en caoutchouc peuvent être tordues et pressées 180 degrés et réintégrer toujours leur forme en quelques secondes,"Selon les experts de l'industrie. Cette résilience les rend idéaux pour des environnements exigeants comme les zones de construction et les autoroutes.
Ajout de caractéristiques de réflexion et de sécurité
La dernière étape consiste à améliorer la visibilité du cône et les caractéristiques de sécurité du cône. Bright colors, comme l'orange ou le rouge, sont appliqués à la surface à l'aide de colorants ou de revêtements. Ces couleurs sont choisies pour leur haute visibilité, s'assurer que les cônes se démarquent dans diverses conditions d'éclairage.
Pour améliorer la visibilité nocturne, Des bandes réfléchissantes sont ajoutées. Ces bandes reflètent la lumière des phares du véhicule, Rendre les cônes visibles même dans les paramètres de faible luminosité. Le matériau réfléchissant est en toute sécurité lié à la surface du cône pour éviter les pelage ou la décoloration avec le temps.
Certains fabricants intègrent des matériaux recyclés dans le processus de production, Réduire les déchets et promouvoir la durabilité. Par exemple, Des bits de pneu moulu peuvent être utilisés à la base du cône, offrant un poids et une stabilité supplémentaires. Cette approche écologique réduit non seulement les coûts de production, mais prolonge également le cycle de vie des produits en caoutchouc jetés.
En combinant un design réfléchi, techniques de durcissement avancées, et améliorations de la sécurité, Les fabricants créent des cônes de sécurité en caoutchouc qui répondent aux normes les plus élevées de performance et de fiabilité. Optsignes de sécurité cônes ne font pas exception, Offrir une durabilité et une stabilité exceptionnelles dans les environnements les plus exigeants. Avec une visibilité et une flexibilité supérieures, OpTsignens fournit une solution de gestion du trafic fiable pour une utilisation temporaire et à long terme.
Considérations environnementales dans la production de cône de sécurité en caoutchouc
La production de cônes de sécurité en caoutchouc joue un rôle essentiel dans le maintien de la sécurité sur les routes et les chantiers de construction. Cependant, Cela soulève également d'importantes questions environnementales. Comprendre les défis et les solutions dans la production durable en caoutchouc peut vous aider à apprécier les efforts pour minimiser son impact écologique.
Défis de durabilité dans la production de caoutchouc
Production de caoutchouc, Qu'il soit naturel ou synthétique, présente plusieurs défis de durabilité. Le caoutchouc naturel repose fortement sur le Hevea Brassilensis arbre, qui pousse dans les régions tropicales. Les plantations en caoutchouc en expansion conduisent souvent à la déforestation, menacer la biodiversité et perturber les écosystèmes. En plus, Le processus agricole nécessite d'importantes ressources en eau et en énergie, Doutrage davantage de l'environnement.
Caoutchouc synthétique, d'autre part, dépend des industries pétrochimiques. Sa production implique de raffiner le pétrole brut, qui contribue aux émissions de gaz à effet de serre. L'extraction et le traitement des composés à base de pétrole consomment également de grandes quantités d'énergie. Ces facteurs rendent le caoutchouc synthétique moins respectueux de l'environnement par rapport à son homologue naturel.
Pour relever ces défis, L'industrie du caoutchouc a commencé à adopter des pratiques innovantes. Par exemple, le Projet en caoutchouc vert par Vibracoustic se concentre sur l'identification des sources durables de caoutchouc et la réduction des substances dangereuses dans les composés de caoutchouc. En améliorant les méthodes agricoles et en explorant des matériaux alternatifs, Les fabricants visent à réduire l'empreinte carbone de la production de caoutchouc.
“La progression des innovations technologiques et l'adhérence à des normes environnementales strictes peuvent atténuer considérablement l'empreinte écologique de la production de caoutchouc,” Selon des études sur les pratiques en caoutchouc durables.
Recyclage et réutilisation des cônes de sécurité en caoutchouc
Recyclage des produits en caoutchouc, y compris les cônes de sécurité, offre une solution pratique pour réduire les déchets. Lorsque les cônes en caoutchouc deviennent endommagés ou usés, Le recyclage les empêche de se retrouver dans les décharges. Ce processus nécessite moins d'énergie par rapport à la production de nouveaux caoutchouc, En faire une option respectueuse de l'environnement.
Le caoutchouc recyclé peut être réutilisé pour diverses applications. Par exemple, Le caoutchouc moulu à partir de vieux cônes peut être utilisé dans les surfaces des aires de jeux, Tracks athlétiques, ou même comme matériel pour les nouveaux cônes de circulation. Certains fabricants intègrent des bits de pneus recyclés dans la base des cônes de sécurité, améliorer leur stabilité tout en favorisant la durabilité.
En soutenant les programmes de recyclage et en choisissant des produits fabriqués à partir de matériaux recyclés, vous contribuez à un avenir plus durable. Cônes de sécurité en caoutchouc, lorsqu'il est produit et éliminé de manière responsable, démontrer comment les outils essentiels peuvent s'aligner sur les objectifs environnementaux.
Les cônes de sécurité en caoutchouc montrent la polyvalence et la durabilité remarquables du caoutchouc. Ces cônes, fabriqué à partir de caoutchouc naturel ou synthétique, Combinez des méthodes traditionnelles avec des techniques modernes pour assurer leur fiabilité. Leurs couleurs vives et leurs caractéristiques réfléchissantes améliorent la visibilité, les rendre indispensables pour maintenir la sécurité dans des environnements dynamiques. Si guider le trafic, Marquage des zones de construction, ou organiser des espaces publics, Les cônes de circulation jouent un rôle essentiel dans la promotion de l'ordre et la réduction des risques. En comprenant leurs origines et leurs applications, Vous pouvez apprécier comment ces outils simples mais efficaces contribuent à la sécurité et à l'efficacité quotidiennes.