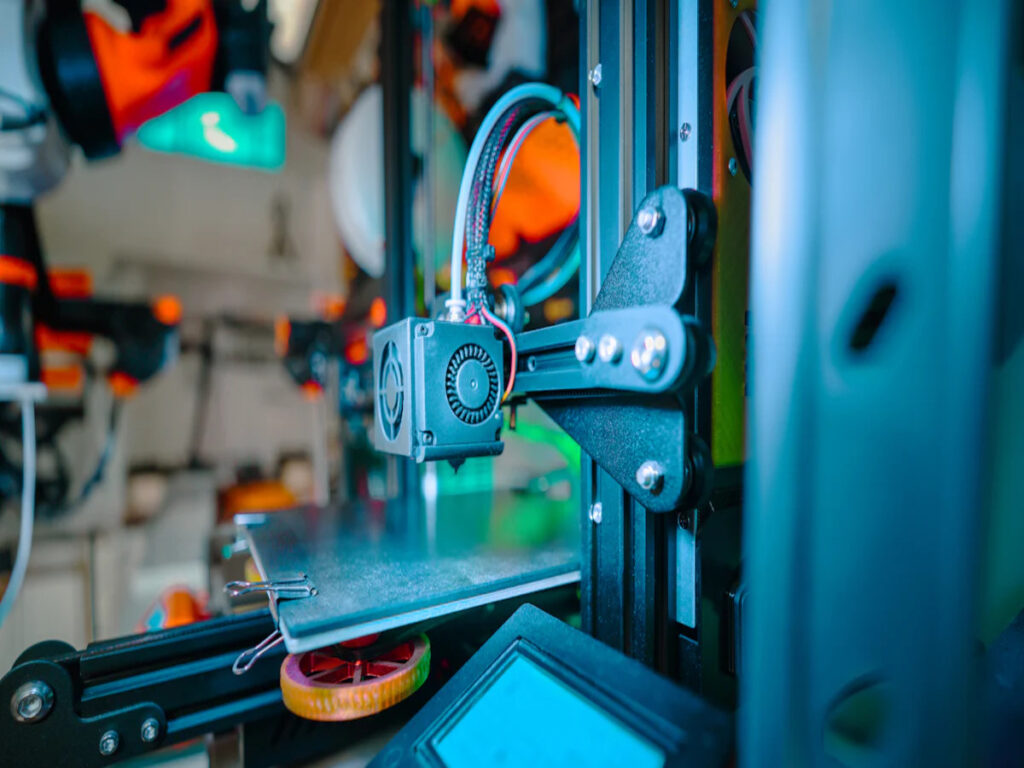
You’ve likely seen how traditional manufacturing often struggles with efficiency and adaptability. 3D Impression has revolutionized this landscape by enabling faster production, reduced waste, and innovative designs. Par exemple:
- It supports decentralized, on-demand production, making manufacturing accessible globally.
- Complex designs can now be created with minimal material waste, Amélioration de l'efficacité.
- Pendant COVID-19 pandemic, 3D printing addressed supply chain issues by providing alternative parts.
For road cone manufacturers, this technology opens doors to unprecedented innovation. You can now create customized cones with unique features, comme integrated sensors ou Lumières LED, while reducing production costs. The global 3D printing market, valued at $20.3 milliards dans 2023, reflects its growing adoption across industries, including road safety equipment.
3D Printing and Its Role in Road Cone Manufacturing
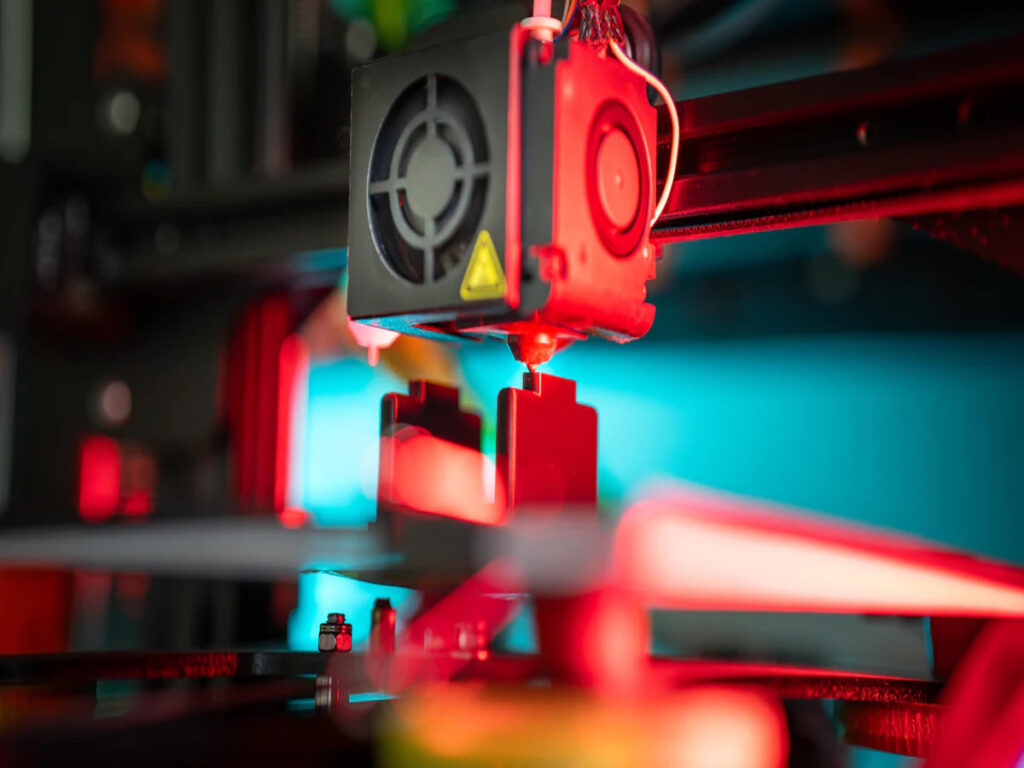
What is 3D Printing?
3D Impression, also called additive manufacturing, is a process that creates three-dimensional objects by adding material layer by layer. Unlike traditional methods that cut or mold materials, this approach builds objects from the ground up, reducing waste and allowing for intricate designs. The process begins with a CAD (Computer-Aided Design) file, which acts as a blueprint. This file is converted into a format the printer can read, and the object is then built using techniques like melt extrusion ou light polymerization. After printing, the object undergoes post-processing and inspection to ensure quality.
For road cone manufacturers, this technology offers a way to produce road safety cones with precision and efficiency. You can create complex designs or prototypes without the need for expensive molds, making it a game-changer in the industry.
The Importance of 3D Printing in Road Construction
3D printing in road construction is transforming how infrastructure is built. Countries like China, the United States, and Dubai are already using this technology for projects such as 3D-printed bus stops and pedestrian bridges. These innovations demonstrate the versatility of 3D printing in creating durable and customized structures.
This technology also allows for the integration of smart features. Par exemple, 3D-printed roads can include embedded sensors that provide real-time updates on traffic and weather conditions. By tailoring designs to specific geographic and climatic needs, 3D printing creates more resilient infrastructure. Ongoing research into eco-friendly materials further enhances its potential, making it a sustainable choice for construction projects.
How 3D Printing Technology Benefits Road Cone Manufacturers
3D printing technology offers several advantages for road cone manufacturers. D'abord, it reduces production costs by eliminating the need for molds and minimizing material waste. This makes it ideal for small-batch or customized production. Deuxième, it enables faster prototyping. You can test new designs quickly, allowing for rapid innovation. Troisième, it supports the creation of unique features, such as road safety cones with integrated LED lights or sensors.
En plus, 3D-printed parts can be produced with high precision, ensuring consistent quality. This precision is crucial for road cones, which must meet strict safety standards. By adopting 3D printing, you can stay ahead in a competitive market while contributing to more sustainable manufacturing practices.
The Evolution of 3D Printing in Road Cone Production
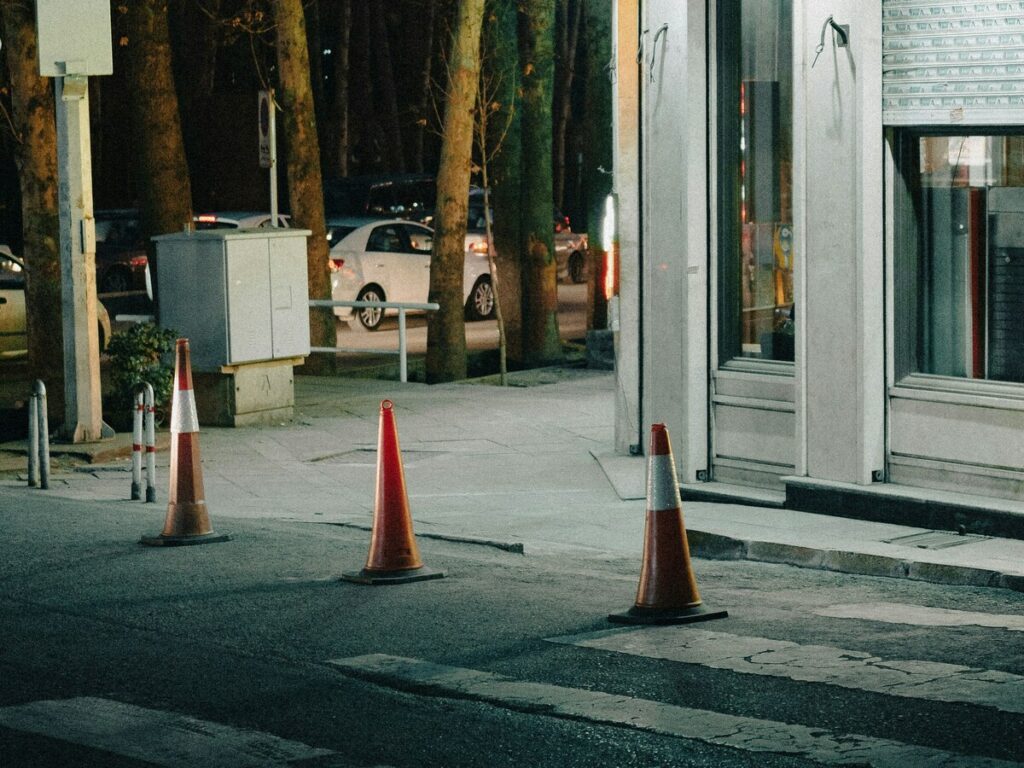
Early Adoption by Road Cone Manufacturers
You might wonder when road cone manufacturers first started using 3D printing. Early adopters saw its potential to streamline production and reduce costs. Initialement, manufacturers used it for prototyping. Instead of relying on traditional molds, they could create prototypes quickly and test new designs. This saved time and allowed for faster innovation.
Some companies also experimented with small-scale production. They used 3D printing to produce limited batches of customized cones. These road safety cones often featured unique designs, such as company logos or reflective patterns. By adopting this technology early, these manufacturers gained a competitive edge. They demonstrated how 3d printing could transform the industry.
Key Milestones in the 3D Printing Revolution
The 3D printing revolution brought significant advancements to manufacturing. One major milestone was the development of stronger and more durable materials. These materials made it possible to create road cones that could withstand harsh weather and heavy use. Another breakthrough was the improvement in printing speed. Faster printers allowed manufacturers to produce more road safety cones in less time.
The introduction of multi-material printing was another game-changer. This technology enabled the creation of road safety cones with integrated features, comme les lumières LED ou les capteurs. These milestones showed how 3D printing could go beyond simple designs and offer advanced functionality. Each step in the 3D printing revolution brought new opportunities for innovation.
Current Applications of 3D Printing in Road Cone Manufacturing
Aujourd'hui, 3D printing plays a vital role in road cone manufacturing. You can use it to create road safety cones with complex designs that traditional methods cannot achieve. Par exemple, some manufacturers produce foldable cones for easy storage. Others design cones with built-in sensors to monitor traffic conditions.
This technology also supports sustainable practices. By using only the material needed, 3D printing reduces waste. Some manufacturers even use recycled materials to create eco-friendly cones. En plus, you can produce prototypes faster than ever before. This allows you to test new ideas and bring innovative products to market quickly. The current applications of 3d printing highlight its versatility and potential to reshape the industry.
Benefits of 3D Printing for Road Cone Manufacturers
Cost Efficiency and Reduced Waste
You can significantly lower production costs by adopting 3D printing in road construction. Traditional manufacturing often requires expensive molds and generates excess material waste. En revanche, 3D printing uses only the material needed, reducing waste and saving money. This efficiency makes it ideal for producing small batches or customized parts.
Par exemple, road cone manufacturers can create prototypes without investing in costly molds. This allows you to test designs quickly and refine them before mass production. En plus, the precision of 3D printing ensures consistent quality, minimizing the need for rework. By optimizing material usage and streamlining production, you can achieve cost savings while maintaining high standards.
Customization and Design Flexibility
3D printing technology offers unparalleled options de personnalisation. You can create one-of-a-kind parts tailored to specific needs, such as road safety cones with unique shapes, couleurs, or logos. This flexibility allows you to meet diverse customer demands and stand out in the market.
Unlike traditional methods, 3D printing enables the creation of complex designs without additional costs. Par exemple, you can produce mass-customized cones with integrated features like LED lights or sensors. These innovations enhance functionality and improve safety in construction zones. With 3D printing, you can push the boundaries of design and deliver products that meet modern requirements.
Optsignes Cônes de trafic support full customization, ensuring that each product not only meets functional needs but also reflects your branding. Whether you need a particular color, logo, or additional features like reflective strips, Signes OPT makes it possible to create road safety cones that are not only effective but also unique to your brand’s identity.
Sustainability and Eco-Friendly Practices
3D printing aligns with sustainability goals by promoting eco-friendly practices. It minimizes material waste by using only what is necessary for production. This approach contrasts with traditional methods that cut away excess material. En plus, 3D printing consumes less energy, reducing carbon emissions during manufacturing.
Localized production further supports sustainability. You can produce road cones near their point of use, cutting down on transportation emissions. Some manufacturers even use biodegradable materials like bioplastics, making their products more environmentally friendly. By adopting 3D printing in road construction, you contribute to a greener future while meeting industry demands.
Par exemple, industries like automotive and healthcare have already embraced 3D printing for its sustainable benefits. Companies use it to create lightweight components and custom-fitted products, reducing energy consumption and material waste. These practices demonstrate the advantages of 3D printing in achieving both innovation and sustainability.
Faster Prototyping and Innovation
You can accelerate the process of creating and testing new designs by using 3D printing. Traditional manufacturing often requires weeks to produce a prototype. This delay slows down innovation and increases costs. With 3D printing, you can create a prototype in hours instead of weeks. This speed allows you to test multiple designs quickly and refine them based on feedback.
Imagine you want to develop a road cone with unique features, such as built-in sensors or foldable designs. Dans le passé, you would need to invest in expensive molds and wait for production to finish. Maintenant, 3D printing eliminates these barriers. You can print a prototype, test its functionality, and make adjustments without wasting time or resources.
This technology also supports experimentation. You can explore new materials, formes, and features without committing to large-scale production. Par exemple, you might test a cone made from recycled materials or one with advanced reflective properties. By experimenting with different options, you can discover innovative solutions that meet customer needs.
Faster prototyping also encourages collaboration. You can share digital designs with your team or clients, gather input, and make changes in real time. This process ensures that the final product aligns with expectations. En plus, the ability to produce prototypes quickly fosters creativity. You can push the boundaries of design and deliver products that stand out in the market.
By embracing 3D printing, you gain a competitive edge. Faster prototyping reduces time-to-market, enabling you to respond to trends and customer demands more effectively. This approach not only saves time but also drives innovation in road cone manufacturing.
Challenges in Implementing 3D Printing in Road Cone Manufacturing
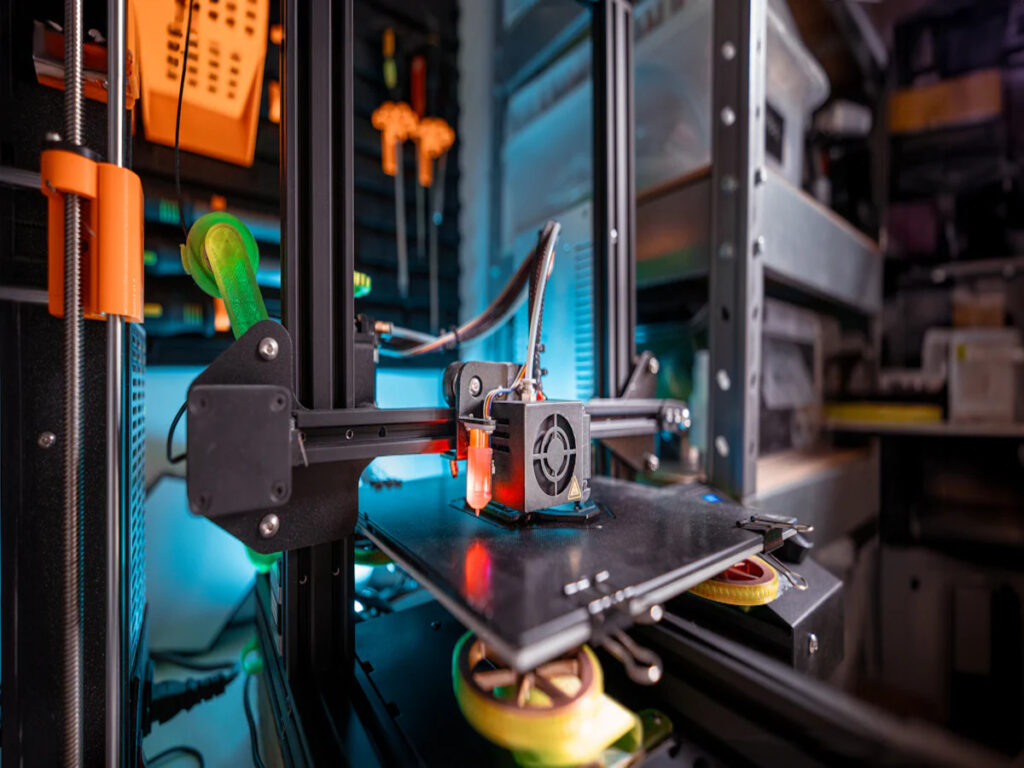
Material Limitations and Durability Issues
You may face challenges with materials when using 3D printing for road cone production. Many 3D printing materials lack the durability required for outdoor use. Road cones must endure harsh weather, Exposition aux UV, and heavy impacts. Traditional materials like rubber or PVC offer these qualities, but finding 3D printing materials with similar properties can be difficult.
Some manufacturers experiment with advanced polymers or composites to improve durability. Cependant, these materials often come at a higher cost. You might also encounter issues with heat resistance. In hot climates, road cones made from certain 3D printing materials may warp or degrade over time. Addressing these limitations requires ongoing research and testing to identify suitable materials for construction environments.
Scalability for Mass Production
Scaling up 3D printing for mass production presents another challenge. While 3D printing excels at creating prototypes or small batches, producing thousands of road cones can be time-consuming. Traditional manufacturing methods, like injection molding, remain faster for large-scale production.
You might also find that the cost of operating multiple 3D printers adds up quickly. Each printer requires maintenance, energy, and skilled operators. To overcome this, some manufacturers explore hybrid approaches. They use 3D printing for custom designs or prototypes and rely on traditional methods for mass production. Balancing these techniques can help you meet both efficiency and customization goals.
Regulatory and Safety Compliance
Road cone manufacturers must adhere to strict safety standards. These regulations ensure that cones perform reliably in construction zones and other high-risk areas. When using 3D printing technology, you must verify that the materials and designs meet these requirements.
Par exemple, reflective road cones must maintain visibility under various lighting conditions. They must also withstand impacts without breaking apart. Testing 3D-printed cones for compliance can be time-intensive and costly. En plus, some regions have specific rules about the materials used in construction equipment. Staying informed about these regulations is essential to avoid setbacks and ensure product safety.
High Initial Costs and Training Needs
Adopting 3D printing technology for road cone manufacturing requires a significant upfront investment. You need to purchase advanced 3D printers, which can cost tens of thousands of dollars depending on their capabilities. High-end printers designed for industrial use often come with additional expenses, such as maintenance contracts and software licenses. These costs can be a barrier, especially if you are a small or medium-sized manufacturer.
Conseil: Start with a cost-benefit analysis to determine if 3D printing aligns with your production goals.
Beyond equipment, you must also invest in training your workforce. Operating 3D printers requires specialized skills. Your team needs to learn how to create and modify CAD files, troubleshoot printer issues, and perform post-processing tasks. Training programs can be expensive and time-consuming, especially if your employees are unfamiliar with digital manufacturing.
You might also face challenges in hiring skilled professionals. The demand for 3D printing experts has grown rapidly, creating a competitive job market. Offering attractive salaries and benefits may be necessary to recruit and retain talent.
To manage these challenges, consider starting small. You could begin by using 3D printing for prototyping or limited production runs. This approach allows you to test the technology without committing to large-scale investments.
Note: Partnering with 3D printing service providers can help you reduce initial costs. These companies offer on-demand printing, allowing you to explore the technology without purchasing equipment.
While the initial costs and training needs may seem daunting, they represent an investment in innovation. By embracing 3D printing, you position your business for long-term growth and competitiveness in the evolving road cone manufacturing industry.
Future Trends in 3D Printing for Road Cone Manufacturers
Advancements in Smart Materials
The future of 3D printing holds exciting possibilities with the development of smart materials. These materials adapt to environmental conditions, making them ideal for road cone manufacturing. Imagine reflective road cones that change color based on temperature or light levels. This feature could improve visibility during different times of the day. Researchers are also exploring self-healing materials. These materials repair minor damages, extending the lifespan of road cones.
Smart materials also enhance durability. Par exemple, advanced polymers resist UV rays and extreme weather. This ensures that reflective road cones remain functional in harsh construction environments. By adopting these innovations, you can create products that meet modern safety and performance standards.
Integration of IoT in 3D-Printed Road Cones
The integration of IoT (Internet des objets) technology is transforming 3D printing in road construction. IoT-enabled road cones can communicate with other devices, providing real-time data on traffic and construction zones. Par exemple, cones equipped with sensors can alert drivers to hazards ahead. This improves safety for both workers and motorists.
You can also use IoT to monitor the condition of road cones. Sensors detect wear and tear, allowing you to replace damaged cones before they fail. This reduces maintenance costs and ensures consistent performance. By combining IoT with 3D printing, you can produce cônes intelligents that enhance efficiency and safety in construction projects.
Eco-Friendly and Recyclable Designs
Sustainability is a key focus in the future of 3D printing. Eco-friendly practices are becoming more important in road construction. You can use biodegradable materials to create recyclable road cones. This reduces waste and supports environmental goals.
Localized production also contributes to sustainability. By printing reflective road cones near construction sites, you minimize transportation emissions. Some manufacturers are even experimenting with recycled plastics. These materials lower production costs while promoting eco-friendly practices. By embracing these trends, you can align your business with global sustainability efforts.
Automation and AI in 3D Printing Processes
Automation and intelligence artificielle (IA) are transforming how you approach 3D printing. These technologies simplify complex tasks, improve efficiency, and open new possibilities for innovation. By integrating automation and AI, you can streamline production and achieve higher precision.
Another exciting application is predictive maintenance. AI monitors the condition of your 3d printers and predicts when maintenance is needed. This prevents unexpected breakdowns and extends the lifespan of your equipment. You can also use AI to manage inventory. Smart systems track material usage and alert you when supplies run low.
3D printing has revolutionized how you approach road cone manufacturing. It reduces material waste and energy consumption, making it a sustainable choice for construction. By using only the necessary materials, this technology aligns with eco-friendly practices while lowering production costs. You can also create durable, customized cones that improve safety and efficiency in construction zones.
The future of 3D printing in road construction looks promising. Advancements in smart materials and IoT integration will redefine how road cone manufacturers innovate. By embracing these trends, you can lead the industry toward a sustainable and efficient future.